SMED, or Single Minute Exchange of Dies, is the technique of reducing the amount of time to change a process from running one specific type of product to another. The purpose for reducing changeover time is not for increasing production capacity, but to allow for more frequent changeovers in order to increase production flexibility. Quicker changeovers allow for smaller batch sizes.
The benefits of quick changeover include:
• Reduce defect rates - Quick Changeover reduces
adjustmentsas part of setup and promotes quality on the
first piece.
• Reduce inventory costs - Elimination of, or reduction in
numbers of batches, and their sizes, allows for recovery of
operating cash and manufacturing space.
• Increase production flexibility - Increase output and
improve timeliness of response to customer orders.
• Improve on-time delivery - Quick Changeover supports
the ability to meet customer demands.
The terms set-up and changeover are sometimes used interchangeably however this usage is incorrect. Set-up is only one component of changeover. Changeover can be divided into the 3 Ups:
Clean-up - the removal of previous product, materials and
components from the line.
Set-up - the process of actually converting the equipment.
Start-up - the time spent fine tuning the equipment after it
has been restarted.
The keys to quick changeover are found in changing your thinking about changeover as in the following:
1. Rethink the idea that machines can be idle, but workers
cannot be idle.
2. The ideal setup change is no setup at all or within
seconds.
3. Ensure that all tools are always ready and in perfect
condition.
4. Blow a whistle and have a team of workers respond to
each changeover.
5. Establish goals to reduce changeover times, record all
changeover times and display them near the machine.
6. Distinguish between internal and external setup activities
and try to convert internal to external setup.
To start identify and separate the changeover process into key operations – External Setup involves operations that can be done while the machine is running and before the changeover process begins, Internal Setup are those that must take place when the equipment is stopped. Aside from that, there may also be non-essential operations. Use the following steps to attack the quick changeover:
Eliminate non-essential operations – Adjust only one side of guard rails instead of both, replace only necessary parts and make all others as universal as possible.
Perform External Set-up – Gather parts and tools, pre-heat dies, have the correct new product material at the line… there's nothing worse than completing a changeover only to find that a key product component is missing.
Simplify Internal Set-up – Use pins, cams, and jigs to reduce adjustments, replace nuts and bolts with hand knobs, levers and toggle clamps… remember that no matter how long the screw or bolt only the last turn tightens it.
Measure, measure, measure – The only way to know if changeover time and startup waste is reduced is to measure it!
Ron Pereira from the Gemba Academy authored a video on Quick Changeover. A great summary of quick changeover is shown below:

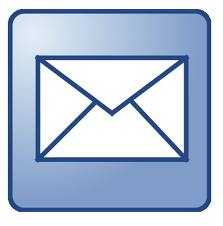





Hi Tim,
ReplyDeleteNice brief summary for those looking into quick setup techniques. In addition to the fine points offered here, may I add that setup time is defined from the last good part (A) run to the next good part (B) run. In this way, we do not forget about the wastes associated with approvals, fine tuning, adjustments, guessing, trialing, etc. This is especially true with make-ready times in printing and other continuous process industries that differ from stamping or molding operations.
Best regards,
Bryan Lund, www.twiservice.com
Great post, Tim. SMED is very important. One thing to remember is seconds count. Sometimes people want to argue it isn't worth doing because it only saves 5 seconds. Over a course of a year 5 seconds can add up significantly. Any little bit of time you can save is worth saving.
ReplyDeleteTim,
ReplyDeleteExcellent post and comments from your readers. SMED is a great tool that can take hours off of a change-over. It's a great way to reduce the effort and time required.
Chris
Bryan, thanks for contributing the definiton of set-up time. That is what I am familiar with since we run continuous processes in about half our plant.
ReplyDeleteMatt, I agree seconds matter especially compounded. In our cable plant we found at our bottleneck process we spend 50% of the total time on set-up. Think of the throughput we can gain and it comes at no cost.
Thanks Christian. I also think set-up reduction is vital for flexibility, low inventory, and capacity.
hey...very nice thanks. Can u pls elobrate on post changeover stablization time...it wud be very helpfull..
ReplyDeletethanks in advance..:)
Raj, I am not sure what you are calling changeover stabilization time. The point of quick changeover is that there is minimal time to change from one product to another so there is no stabilization time.
DeleteWhat type of process are you thinking of?
ya...Tim actually its a finishing line in which post to a changeover after the line starts different types of Down Time comes and adjustments have to be made. So, we call it as line is not stablized. But after a point of time all the settings being done during changeover gets set for that SKU and we say it as line is stablized. So my question is:
ReplyDelete1. At what point we can say that Changeover is completed.?
2. At what point we can say that a line is stablized ..??
Raj, this is more more clear. Similar to my background with extrusion where we changed materials and colors. There was a period of time for the consistency of the material flow and the color changes to bleed through. In my experience we did not change the definition for linear continuous flow production from that of discrete piece part production. Changeover is defined at the time from the end of the last good part to the beginning of the first good part. The problem is probably not in knowing when you are done but rather when it is good. Well, you need to develop standards. For instance in the color changes of a cable you would need to bleed through from one to another. We developed color standards so you would know when you were are the standard color and could therefor go to the good spool. Without this standard the time changed but more importantly the quality of the the cable color.
DeleteOne other point I would make is the time is not the important part. All you need is a consistent measure by which to make and measure improvements. Remember the goal is not the accuracy of the the changeover time but rather the improvement of the changeover process so it can be done quicker.
Tim, great post! We are working on a post about changeover for our blog and are wondering if you would be able to contribute? Keep it up!
ReplyDelete