----------------------------------------------------------------------------------
The Shingo model, while relatively unknown outside of manufacturing, is not just a model for understanding or improving manufacturing processes. It is a comprehensive system of management that incorporates both cultural and tactical, operational elements to bring about culture change and improved effectiveness. In the Shingo model, Guiding Principles determine the values of the organization, which lead to the development of processes and the usage of tools, as needed, to deliver results. It is not the just the implementation of tools to get a specified result – it is a reinforcing dynamic between both tools and culture. The two are taken together to form a comprehensive paradigm for workplace transformation that addresses, directly, both the need for culture to change and the need for the business to perform so that one may sustain the other. In fact, it was in a workshop put on by the Shingo prize organization where I first heard the term “Old culture plus new tools = same results.”
Some time after my introduction to Lean and the Shingo model, I discovered the Results Only Work Environment (ROWE) concept. ROWE is a practice created at Best Buy’s headquarters in Minneapolis that allows employees to work where they want, when they want, and how they want – as long as the work gets done. In their book, “Work Sucks and How to Fix It” Cali Ressler and Jody Thompson describe the reasons why they developed ROWE and how it was implemented. In the book, they state:
“We’re offering not a new way of working, but a new way of living. This new way of living is based on the radical idea that you are an adult. It’s based on the radical idea that even though you owe your company your best work, you do not owe them your time or your life…..The book goes on to lay out the rest of what ROWE is based on, at its core: The myth that time + physical presence = results. The authors also identify several things that make a ROWE work, centering on building behaviors that create trust between managers and employees. Among these are things such as all meetings are optional, people will stop doing anything that wastes time - theirs, the company’s, or the customers’, there are no last-minute fire drills and nobody brags about how many hours they work (and especially not about how many hours they worked for the sake of just showing up and looking good without producing much of anything.)
In a Results-Only Work Environment, people can do whatever they want, whenever they want, as long as the work gets done. Many companies say their people can telecommute or work a flexible schedule. But these arrangements often still include core hours, or can be dissolved should business needs change or are doled out stingily as a perk for the privileged few. In a ROWE, you can literally do whatever you want whenever you want as long as your work is getting done. You have complete control over your life as long as your work gets done.”
Those aspects of ROWE sound a lot like what Lean thinkers would easily and readily identify as waste, and it is encouraging to see that wasteful practices are so easily spotted by people with no Lean or manufacturing background. Although ROWE, in my mind, has a weakness in that it doesn’t offer a system for continuous improvement such that the tremendous cultural awakening it generates can be sustained, I don’t think that ROWE is inconsistent with Shingo’s teachings, either. In fact, I think ROWE in many ways takes the cultural aspects of these teachings, especially the Respect for People foundation of the Shingo model, to a whole new level of understanding.
Respect for People needs to be an absolute. It’s not just Respect for Workers (meaning we only offer respect to a person when they walk in the door to go to work), it’s respect for the person. The person, of course, has needs, wants and desires that existed long before they ever came in to work and that will go on long after. If Lean and Shingo are about trusting front-line workers to the point that they can determine for themselves the best way to go about their work, then ROWE is simply taking that concept further. It is saying that not only should workers be given the respect and freedom to optimize their own work, but their lives as well – which may very well mean that individuals can also decide when and where they get their work done, too.
Obviously, the ROWE concept is easier to conceive of in knowledge work environments, where work products are a bit more intangible, less dependent upon facilities and large capital equipment, and where technology has developed to the point that work products can be transferred from producer to customer from nearly anywhere. Given that ROWE was created in white-collar space by Human Resources professionals, it is strongest in that area, much as Shingo, which began in manufacturing, is strongest in that area. There is nothing to say, however, that the concepts can’t be applied to other areas. In a manufacturing setting, for example, trusting the personnel in the supply chain, assembly, and shipping functions to coordinate, carry out their tasks, arrive at the plant, produce the units and deliver 10,000 widgets by the 18th of the month is entirely consistent with ROWE’s teaching. ROWE is not entirely about working any time, any where, it is about trusting people to do their jobs without being baby sat.
Other concepts that form the basis of ROWE are very similar to those in the Shingo model, particularly with regards to Culture, Guiding Principles and Results. The Shingo model is much stronger, however, when it comes to identifying the specific systems and tools that help to reinforce and build up the cultural elements. In this respect, the ROWE concept feels a bit incomplete. While it certainly embraces and evolves the humanistic concerns and personal motivations that result in employee engagement, the Shingo Model’s greater emphasis on methods for Continuous Process Improvement and Enterprise Alignment offer guidance on how to sustain it.
About the Author:
David M. Kasprzak is the author and creator of the My Flexible Blog, where he shares his thoughts on improving workplace culture through the use of Lean concepts. While working as an analyst to develop and analyze program-level cost and schedule metrics for the past 12 years, David has now turned his attention towards understanding the behaviors that create high-performing organizations. In May of 2011, he received my MBA degree with a concentration in Marketing & Strategy.

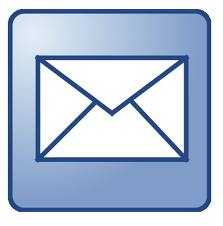





Would be interested to know if "resource constraints" could wind up over-taxing people who have to do "whatever it takes to get the work done" with no support.
ReplyDelete