For my Facebook fans you already know about this great feature. But for those of you that are not connected to A Lean Journey on Facebook or Twitter I post daily a feature I call Lean Tips. It is meant to be advice, things I learned from experience, and some knowledge tidbits about Lean to help you along your journey. Another great reason to like A Lean Journey on Facebook.

Click this link for A Lean Journey's Facebook Page Notes Feed.
Here is the next addition of tips from the Facebook page:
Lean Tip #436 - Management must go to the Gemba to practice Lean management.
Go see for yourself at the place the work is done.
Look at the process and talk with the people.
Ask these three simple questions:
• What is the process?
• How can you tell it is working?
• What are you doing to improve it (if it is working)?
Teaches us to see in new ways what we have failed to see before.
Go see for yourself at the place the work is done.
Look at the process and talk with the people.
Ask these three simple questions:
• What is the process?
• How can you tell it is working?
• What are you doing to improve it (if it is working)?
Teaches us to see in new ways what we have failed to see before.
Lean Tip #437 – Go For Many Small Wins, Rather Than The Occasional Big Win
Small wins keep up the enthusiasm, and certainly add up.
Embed your improvements for lasting change.
Make this “The way we do things around here.”
Management needs to continually recognize small wins.
Small wins keep up the enthusiasm, and certainly add up.
Embed your improvements for lasting change.
Make this “The way we do things around here.”
Management needs to continually recognize small wins.
Lean Tip #438 – Stop Fighting Fires, Think Proactively
Problems (fires) can be avoided and the resulting fire fighting by trying these proactive steps:
• Stop rewarding fire fighting and start recognizing fire preventing.
• Create a corrective and preventative action process based on root cause analysis.
• Conduct follow-ups.
• Share lessons learned.
Problems (fires) can be avoided and the resulting fire fighting by trying these proactive steps:
• Stop rewarding fire fighting and start recognizing fire preventing.
• Create a corrective and preventative action process based on root cause analysis.
• Conduct follow-ups.
• Share lessons learned.
Lean Tip #439 - Map Your Value Stream
Mapping your processes will help you understand the actual condition.
• The actual place or location in which a process occurs
• The actual employees working in that location
• The actual process in that location
A Target is not the same as a Target Condition
Mapping your processes will help you understand the actual condition.
• The actual place or location in which a process occurs
• The actual employees working in that location
• The actual process in that location
A Target is not the same as a Target Condition
Lean Tip #440 – Use a charter to establish the framework of the kaizen.
A charter determines what the problem statement is, relevant background information, time frame, team members, and some estimation of the resources involve.
You must determine how you will measure the success of this kaizen so you know if your countermeasures are effective.
A charter determines what the problem statement is, relevant background information, time frame, team members, and some estimation of the resources involve.
You must determine how you will measure the success of this kaizen so you know if your countermeasures are effective.
Lean Tip #441 - Picking the team members should be an important part of planning the kaizen.
The team members on the kaizen are the brain power and manpower behind the improvement.
Picking the team members should be an important part of planning the kaizen.
You need to consider people's skill sets, expertise or knowledge, individuals within and outside the process, and who will provide the learning.
The team members on the kaizen are the brain power and manpower behind the improvement.
Picking the team members should be an important part of planning the kaizen.
You need to consider people's skill sets, expertise or knowledge, individuals within and outside the process, and who will provide the learning.
Lean Tip #442 - Perfection is elusive.
If you try to achieve perfection you may well be at the kaizen a very long time.
If you can accomplish 80% of what you set out to and meet the goals of the charter then call it complete. You will be back to improve from this new state again.
Failure to follow through on these can undermine the team's efforts.
If you try to achieve perfection you may well be at the kaizen a very long time.
If you can accomplish 80% of what you set out to and meet the goals of the charter then call it complete. You will be back to improve from this new state again.
Failure to follow through on these can undermine the team's efforts.
Lean Tip #443 – Ensure Non-Participants Have Visibility To Kaizen
Getting the buy in from those who are not participating on the team is important for sustaining the improvement.
For those who are not involved we need to make them aware of the improvements the team is making.
If you don't they will naturally resist the improvement.
Getting the buy in from those who are not participating on the team is important for sustaining the improvement.
For those who are not involved we need to make them aware of the improvements the team is making.
If you don't they will naturally resist the improvement.
Lean Tip #444 – Pick a Winning Team for Improvement
Here are a couple of things to consider when picking team members:
• Balance of "hard" and "soft" skills
• Best experience possible
• Coverage of the knowledge areas needed
• Willingness to join, available
• Leadership / Management skills
• Maturity to take responsibility
• Follows through on commitments
• Good listening skills
• Willing to actively participate
• Can give and take feedback
• Can communicate clearly
Here are a couple of things to consider when picking team members:
• Balance of "hard" and "soft" skills
• Best experience possible
• Coverage of the knowledge areas needed
• Willingness to join, available
• Leadership / Management skills
• Maturity to take responsibility
• Follows through on commitments
• Good listening skills
• Willing to actively participate
• Can give and take feedback
• Can communicate clearly
Lean Tip #445 – Great Groups Need Great Leaders
Every great group has a strong and visionary leader. Not simply an ambition to succeed but vision that inspires the team to work as if the fate of civilization rested on their completing their project.
Every great group has a strong and visionary leader. Not simply an ambition to succeed but vision that inspires the team to work as if the fate of civilization rested on their completing their project.
Lean Tip #446 - Focus on Behaviors, Not Results
Performance has a random pattern to it.
Rewards and reprimands don’t change results short term.
Work on changing behaviors and skills.
Performance has a random pattern to it.
Rewards and reprimands don’t change results short term.
Work on changing behaviors and skills.
Lean Tip #447 - Effective Meetings Are a Necessity
Create an agenda and stick to it.
Establish a meeting code of conduct.
Everyone’s idea will be heard.
Use the 3 Knock Rule and a “Parking Lot” for out of scope ideas.
Create an agenda and stick to it.
Establish a meeting code of conduct.
Everyone’s idea will be heard.
Use the 3 Knock Rule and a “Parking Lot” for out of scope ideas.
Lean Tip #448 - Improvement Starts and Ends with Communication
It is crucial to be able to communicate openly and honestly about ideas, recommendations and concerns with other team members.
It is just as important to be able to listen attentively and respond objectively with helpful feedback.
It is crucial to be able to communicate openly and honestly about ideas, recommendations and concerns with other team members.
It is just as important to be able to listen attentively and respond objectively with helpful feedback.
Lean Tip #449 - Give people autonomy.
Give people autonomy.
• Match skills to risk.
Doesn’t apply to negligence.
People learn best in ‘sink or swim’ situations.
• Leaders should act as lifeguards.
Teams should not fear failure.
Give people autonomy.
• Match skills to risk.
Doesn’t apply to negligence.
People learn best in ‘sink or swim’ situations.
• Leaders should act as lifeguards.
Teams should not fear failure.
Lean Tip #450 - Get People the Right Skills to Succeed
Performance requires many factors therefore we must supply minimum skills to meet basic job requirements. Enhancements of skills lead to exceptional performance. Skill building requires resources and a plan.
Performance requires many factors therefore we must supply minimum skills to meet basic job requirements. Enhancements of skills lead to exceptional performance. Skill building requires resources and a plan.

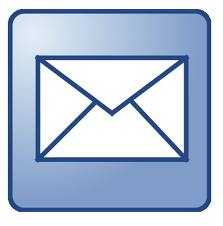





No comments:
Post a Comment