In Bob Emiliani’s recent newsletter he explores the notion of managers as queues:
The method that managers normally use to process information is batch-and-queue. As a result, managers often delay taking action or making decisions. Sometimes the delays are necessary and legitimate, but most are not. Because of batch-and-queue information processing, managers can inadvertently harm efforts by people at lower levels to improve material and information to flow. While we have many Lean tools to improve the technical aspects of material and information flow, we have only education and training to help managers' desire and ability to improve flow in the work processes that they own.In some cases, the manager even intentionally develops a batch process to avoid interruptions. Managers should not have to review everything their team does. Management should not be synonymous with "command and control.”
Everyone would quickly realize that the job of the manager is not "to handle" things (which implies immediately, or nearly so), but instead to delay things and to make people wait. Few managers would think of themselves as queues and would likely justify delays in action or decision-making. Regardless, this is a big problem.So if managers recognize this approach as ineffective why are there still queues:
Why do managers delay things and make people wait? It is because managers are human, which means we are all are subject to the following:The role of a manager like that of a Lean process should be about creating flow and empowering employees. The flow of information enables continuous improvement by applying the PDCA cycle.
- Faulty assumptions
- Illogical thinking
- Decision-making traps
- Overconfidence
- Mistaking beliefs for facts
- Uncertainty
- Distractions (organizational politics)
- Being inflexible
- Status quo oriented
- Making or repeating mistakes
This is indeed what some leaders do when they re-orient themselves from command-and-control to servant leadership. Lean leaders, of course, develop awareness of the many ways they can inhibit flow through participation in kaizen. Not being status quo oriented they seek to improve themselves and their managerial capabilities in ways that are consistent with Lean principles and practices.Managers should systematically be identifying and reducing bottlenecks in their processes. Some fail to notice they may be the source of problems. Managers can set a good example by starting improvement with themselves and how they approach managing.

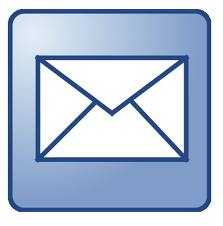





No comments:
Post a Comment