"The best time to train workers is when an error is first detected. It also is the best time to solve a problem." — Dr. Ryuji Fukuda, VP of Production at Sumitomo Electric
When do you train your personnel in problem solving? How do you train them in problem solving? Dr. Ryuji Fukuda, VP of Production at Sumitomo Electrics says "The best time to train workers is when an error is first detected. It also is the best time to solve a problem." He refers to this activity as On-Error-Training (OET).
The following five rules are necessary to make OET work successfully in your shop.
Self Rule – The responsibility of finding the root cause of the problem must be from the worker who first detects the problem. They must stop the line and get their coworkers to help.
Quickly Rule – It is important to solve the problem immediately when the information is right at hand.
Actually Rule – You must replay the process that transpired before the defect occurred and try to re-create the defect. Management must challenge and empower the worker who detected the problem to take the prime role of problem solving in order to learn.
Support Rule – Everyone must stop working and support the primary problem solver in the process of finding the root cause and determining appropriate countermeasures.
Don’t Speak Rule – Management (supervisors and managers) must not come up with all the answers. Allow the discoverer and coworkers the time to discuss the problem and a chance to solve it. If they get stuck then management can offer suggestions.
This simple process will help you reduce quality defects, empower your work force, and create a learning organization. It can only be effective if people are allowed to stop line and eliminate the root cause of the defect. In the long run you will be much better off resolving issues as they occur.

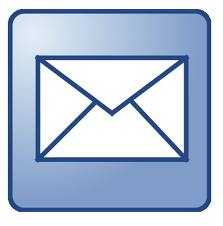





good
ReplyDelete