In June’s post on ASQ’s A View from the Q Blog Paul Borawski asks how you are moving quality beyond product.
… the Quality Council report provides great insights on how the quality community is responding and what it can do better. And therein lies the seed for my question of the day. The opening paragraph of the Quality Council’s perspective is, “For some organizations, ‘quality’ remains a set of tools and techniques associated almost exclusively with quality control. For others, quality has evolved into a critical partner, closely linked with business model development and the enterprise-wide execution of long-term strategy to achieve results.”Building a quality culture is not an easy task. A quality culture starts with managers who understand and believe the implications of the systems view and know the necessity of serving customers in order to succeed. The result of that understanding is a culture where a positive internal environment and the creation of delighted customers go together. It is a culture that naturally emphasizes continuous improvement of processes, one that results in a healthy workplace, satisfied customers, and a growing, profitable company.
Every year companies ratify and formally commit to their quality policies but are they more than words on paper. It should be part of the culture of the company. Employing quality methods and practices in everything you do provides a firm foundation for your business and can be a determining factor in your success.
To create a culture of quality, an organization must align its organizational processes with quality planning and desired outcomes. Quality leadership starts with the leaders who plant the seeds, create the environment for success, empower others and deploy quality throughout the organization.
After safety, quality must be the organization’s highest priority. In lean manufacturing one of the principles we teach is to build in quality. Many think it is only about eliminating waste but that is too minimalistic. Quality issues result in all sorts of waste. As a result, lean principles specifically seek to address this point.
Quality must go beyond our product or service. We cannot add it at the end of the line or inspect it into the product. At best that is only a false sense of security. If we want a quality product it must be made with quality processes by quality minded people. A focus on quality must be intrinsic to the company culture and practices for the customer to take notice.
In my opinion successful businesses are those that not only sell quality to their employees but make it part of the culture or what they do daily. The organization must make quality a top priority for everyone in the company, from top managers to the workers building product. The final product and goal of the organization is creating value for consumers.
A quality organization understands that the realization of quality must be continually energized and regenerated. Successful implementation of a quality focused organization requires commitment and patience, but the rewards are substantial. Beyond the obvious practical benefits, organizations become empowered to solve persistent process and performance challenges while raising the expectations they set for themselves.
It is said that the quality of an organization can never exceed the quality of the minds that make it up. The key to success lies in how well each employee is motivated and inspired to deliver quality work.
I’m part of the ASQ Influential Voices program. While I receive an honorarium from ASQ for my commitment, the thoughts and opinions expressed on my blog are my own.

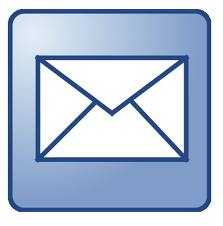





No comments:
Post a Comment