"Mistakes are the portals of discovery." — James Joyce (1882-1914), Irish novelist and poet
One of the premises of Lean is to make it right the first time. The truth is people make mistakes.
In Lean organizations, mistakes are seen as opportunities to improve. There is no blame game if something goes wrong. People are not rewarded for how few mistakes they make, but on how well they improve the process when mistakes have occurred. Management bears the responsibility for creating effective systems that prevent mistakes.
Learning from mistakes clearly needs some analysis of the mistake itself to gain value from it. Here are a few steps to use to analyze a mistake quickly and efficiently:
- Accept that it happened and can’t be changed.
- Know there is always something to learn from it.
- Look to understand it and the factors that caused it.
- How could you have recognized the mistake earlier?
- How can you avoid the mistake next time?
- Are there similar things that might have a related mistake to avoid?
- What has changed now to ensure that mistake doesn’t reoccur?
- Who else should know about this and learn from it?

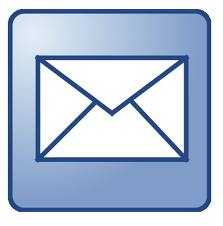





Great Post and true learning as well. lest,we forget - Failures are the stepping stones of Success.
ReplyDeleteGreat post, what drives me crazy is that management don't use all the tool available to teach. In manufacturing I don't see enough work instructions that utilized video. If your still relying on written manufacturing procedures only in 2012 wake up!
ReplyDeletehttp://www.leanplanet.org/
I enjoyed the quote Tim
ReplyDeleteAlong a similar theme:
Some mistakes are too much fun to only make once. ~ Brad Paisley
You never know what you might learn
James