Who are you and what do you do?
My name is Marci Reynolds and I am Vice President of HELP24 Technical/Customer Support for ACI Worldwide, the leading global payments software provider for banks and retailers. I lead an international team of just under 200 employees with offices in the Americas, EMEA and APAC regions. Our vision is to provide the best customer support in the payments industry.
How and when did you learn Process Improvement?
My first introduction to process improvement was in the early 90’s, when I worked at The Boston Globe newspaper where they used the APIMC approach to address business problems. APIMC stands for: analyze, plan, implement measure and control. In the late 90’s, I participated in a Six Sigma wave with another company, was formally trained in the DMAIC process and received my Greenbelt certification. Last year, I got involved with another twist on Six Sigma, which we labeled the “Higher Velocity” approach.
How and why did you start blogging or writing about Process Improvement?
I have been blogging for about 6 years. I started writing about process improvement within sales (i.e. sale enablement) and then switched to process improvement within service operations about 2 years ago (refer to The Operations Blog). I enjoy writing, sharing what I have learned and getting feedback and ideas from the blog readers. It also forces me to keep current with industry trends.
What does Process Improvement mean to you?
It means identifying and taking action to remove the roadblocks and causes that prevent us from fully achieving our business objectives. Process improvement allows us to implement sustainable improvements in results, not band-aid fixes. It is about looking upstream, and thinking about end to end activities, instead of focusing on the end result only.
What is the biggest myth or misconception of Process Improvement?
The biggest myth I have heard is that process improvement (Six Sigma, Lean etc) is only for manufacturing environments. Second, that process improvement can not be used in creative professions, like logo design. In reality, process improvement techniques can be used in any work environment, for any profession and in any industry.
What is your current Process Improvement passion, project, or initiative?
My entire job is about process improvement. Here are some examples of the types of business questions/problems that my team and I are current addressing using systematic, process review techniques: How can we resolve customer cases faster? How can we improve the capacity of our engineering team to implement code fixes? How can we improve collaboration across departments?

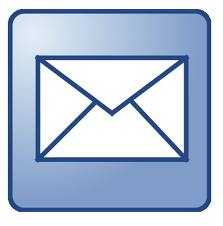





No comments:
Post a Comment