Linda Forshaw is a freelance writer and published author from Liverpool in the UK. She is writer for DegreeJungle.com and specializes in social media, marketing and technology. Contact her on Twitter at @seelindaplay
“The principles of this philosophy are about streamlining processes and making flow more efficient.” - Six Sigma, Aveda Business Institute
Considered a philosophy as much as it is considered a process, Lean Manufacturing is built on the tenet of waste elimination. With an underlying concept of value, the method seeks to add value to a finished consumer product via the elimination of things like time, materials and personnel. Often referred to simply as “Lean,” the method may also focus on providing internal benefit to a company by reducing cost and investment in inventory. The desired result is to maintain a steady production schedule to deliver the optimal quantity of quality goods at the best time and place. In practice, this method of manufacturing is often seen to be mutually beneficial; to create profit and enhance end product quality.
The core ideas surrounding Lean Manufacturing can be traced back as far as the 1800s when Eli Whitney perfected the concept of interchangeable parts. In 1910, Henry Ford took the idea a step further when he arranged all of the elements required for manufacturing the early Model T automobile into one continuous system. His innovation and ability to see that everything from people and machines to tools and products should work together harmoniously has often led Ford to be declared the first practitioner of Lean Manufacturing. The retooling of Ford’s plants for war production saw the Willow Run Bomber plant famously build “A Bomber An Hour.” This notable feat caught the attention of the Toyota Motor Company in Japan. The Japanese industrialists refined Ford’s practices in order to develop the Toyota Production System, commonly referred to as the “Just In Time” system.
By the 1980s, American manufacturers had started to realise the benefits of such a production system. Various acronyms such as World Class Manufacturing (WCM), Continuous Flow Manufacturing (CFM) and Stockless Production have been used, but they essentially all use the same concepts as those seen in the Toyota system. The term “Lean Manufacturing” was first introduced by James Womack in his 1990 book, “The Machine That Changed The World.” The concept has now captured the attention of thousands of manufacturers, with lean implementations in production environments now commonplace. The experience and knowledge base surrounding the technique continues to expand rapidly, helped in part by the growing interest in sustainability and green manufacturing techniques.
Lean manufacturing and sustainability can be seen to go hand in hand. Growing ecological responsibility and an increasing commitment to preserve precious resources for future generations have seen the introduction of many green MBA programs at educational establishments across America and the globe. Until Spring 2012, the Aspen Institute conducted a biennial survey known as Beyond Grey Pinstripes. The resulting data produced a list of the highest ranking green MBA programs in the world. In the 2011-2012 survey, three US universities featured in the highest ranking five establishments. The Stanford Graduate School of Business took top place, with the Mendoza College of Business at the University of Notre Dame taking fourth, and The Yale School of Management coming in at number five.
Individuals seeking a better understanding of the concept of Lean Manufacturing and its correlation with sustainable practices may wish to undertake the free online course from the Aveda Business Institute. For a limited time Six Sigma White Belt Certification is offered free of charge. This offer represents an excellent opportunity for those interested in Lean to benefit from free online education.

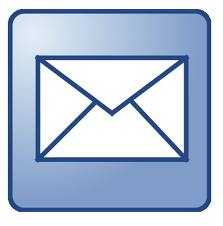





No comments:
Post a Comment