Who are you and what do you do?
My name is Martin Boersema, and I’m a manufacturing engineer in Ontario, Canada. I’m also a continuous improvement coordinator, a kaizen facilitator, lean trainer and a lot of other names. I currently work at a smaller division of a large international automotive parts supplier. One of the benefits of working in a smaller plant, is that I have some autonomy to try different things without wading through reams of red tape.
How and when did you learn Lean?
The origins of Lean are in automotive manufacturing, so I’ve been exposed to it in my daily work for many years. Working in a just-in-time facility forces a lean mentality somewhat, but a lot of our activities are still achieved simply by brute force. Old habits are hard to break and there are plenty of opportunities.
A mechanical engineer by education, I worked for several years in program management, and also dabbled as a six sigma black belt, completing several projects, and learning some lean aspects like value stream mapping.
In my current role of manufacturing engineer, I still use all my six sigma training, doing statistical tests, gauge studies and the occasional Design of Experiments. My primary focus now is on lean activities, where I get to design work cells, and lead small teams in kaizen events.
My first official lean training took place about 10 years ago at a Ford lean workshop. We got to play with a Lego work cell and experience lean concepts. Since then, I’ve become the trainer and conducted similar training using games to show lean concepts.
While not certified in lean (if there is any value in that, I’m not sure), I’ve been mentored by some very knowledgeable lean experts.
How and why did you start blogging or writing about Lean?
I`m a geek. One of my passions outside of work is playing boardgames. I’m not talking about your grandmother’s Parcheesi or the annual Christmas game of Monopoly, but real strategy games where you have to balance scarce resources to achieve long term victory. In my spare time I spend many hours deep in thought staring silently at little cardboard pieces with groups of other similarly crazy people.
Experiencing a lean training game, especially one using Lego, hooked me immediately. It was amazing to see lean concepts in action, but because of my passion for games, I loved the simulation just as much. As I began to train people myself, I looked for more simple and fun ways to demonstrate Lean. I had big plans to design my own version of a lean game and publish it for everyone, so I started my blog.
Well, I haven`t designed my own game yet, but I found a lot of great training material. And the more I read about lean, the more I wrote about it. Now the site has become more than just a collection of resources, but also a chronicle of my own lean journey.
And who knows, I might still put together a lean simulation of my own.
What does Lean mean to you?
Lean for me is a way of thinking. Often I ask myself what is the “Lean” approach to a certain problem. You have to understand the reasons why you’re doing things, the goal behind the tools. This took me awhile to figure out, and I think everyone has to go through this learning process by working on lean projects themselves, not just learning it in a book.
What is the biggest myth or misconception of Lean?
See above. Lean is about reducing inventory, improving flow, linking processes, reducing lead times and improving flexibility. When you’re tasked with a problem, it’s easy to look at that problem, that particular process and see how it can be improved. Sometimes we lose ourselves in addressing an individual process, but there’s no continuity with the rest of the process. And then Lean doesn’t move the business forward significantly.
We need to step back and look at the big picture. How does an improvement fit into the whole? Although individual aspects of lean are often easy and make common sense, Lean as a whole is difficult, since everything is interlinked.
What is your current Lean passion, project, or initiative?
I still work on specific areas and lead kaizen events (I even build the odd flow rack myself), but my current passion is for larger systemic solutions, that improve the entire business. These types of projects, like kanban, visual scheduling, communication improvements take longer and touch more areas in the plant. They’re harder. But the reward is greater.

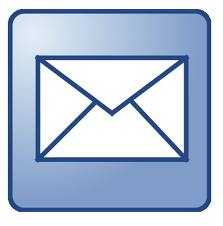





Thanks for featuring this interview on your blog!
ReplyDeleteMartin