Click this link for A Lean Journey's Facebook Page Notes Feed.
Here is the next addition of tips from the Facebook page:
Lean Tip #541 – Productivity Tip: Plan your work, then work your plan.
It is important that you always follow through with what you intend to do, otherwise you are making your plan irrelevant and negating the value of the planning time.
It is important that you always follow through with what you intend to do, otherwise you are making your plan irrelevant and negating the value of the planning time.
Lean Tip #542 – Productivity Tip: Delete whenever possible.
It is important that you frequently revisit your plan and task list. Always cross off the tasks and projects you have completed, and eliminate or delegate those that are no longer important.
Lean Tip #543 – Productivity Tip: Learn to delegate wisely.
When you delegate a task to another person, make sure the person you are delegating it to has clear instructions on how to complete the task, has enough resources for the task, and has the authority to make any decisions that might affect the outcome of the task.
Lean Tip #544 – Productivity Tip: Identify your high-payoff items.
Make sure that you concentrate on the right tasks, which will generate results for you and your company. Stephen Covey suggests first addressing tasks that are both Important and Urgent. Effective time management is not about being busy, but about getting results.
Lean Tip #545 – Productivity Tip: Work from a prioritized action list.
You need to determine what your work priorities are, both short term and long term. I suggest using a standard method like the Formula for Success to prioritize your action list for the greatest success.
You need to determine what your work priorities are, both short term and long term. I suggest using a standard method like the Formula for Success to prioritize your action list for the greatest success.
Lean Tip #546 - Set aside time each week to actively and openly nurture the lean journey in your organization.
You must understand that one of your most important jobs as a lean manager is to develop and nurture other lean thinkers and to do this you must be engaged with them on a regular basis and be willing to put a high priority on improvement activities for yourself and others.
You must understand that one of your most important jobs as a lean manager is to develop and nurture other lean thinkers and to do this you must be engaged with them on a regular basis and be willing to put a high priority on improvement activities for yourself and others.
Lean Tip #547 - Get out of your office and walk the value stream at least once per week.
There is no better way to experience the flow of value (or lack thereof) than taking the same journey that an order, new product, patient or other takes through your processes. Start where the order, product or person enters your value stream and "go see" all the places they go from start to finish. Look for all forms of the 7 wastes and when you see them, think about "why" they exist. Do this often in order to gain a true understanding of your processes. What happens on Monday is not necessarily what happens on Friday. See if you can discover why on your Gemba walks.
There is no better way to experience the flow of value (or lack thereof) than taking the same journey that an order, new product, patient or other takes through your processes. Start where the order, product or person enters your value stream and "go see" all the places they go from start to finish. Look for all forms of the 7 wastes and when you see them, think about "why" they exist. Do this often in order to gain a true understanding of your processes. What happens on Monday is not necessarily what happens on Friday. See if you can discover why on your Gemba walks.
Lean Tip #548 - Use your eyes and ears more than your vocal chords when on the shop floor.
Shigeo Shingo noted that improvements come from the "common sense and experience of the people who do the work". You need to look and listen to what the many intelligent, creative people who make your business run have to say about what goes on in their world each day. If you don't do this regularly how will you have a prayer of knowing how to support their improvement efforts or gain their trust and commitment to change for the long haul?
Shigeo Shingo noted that improvements come from the "common sense and experience of the people who do the work". You need to look and listen to what the many intelligent, creative people who make your business run have to say about what goes on in their world each day. If you don't do this regularly how will you have a prayer of knowing how to support their improvement efforts or gain their trust and commitment to change for the long haul?
Lean Tip #549 - Ask 5 different people who work for you "what can be improved" at least once a week.
This may sound simple but if you ask, you must also be prepared to offer support and provide time and resources to allow them to make the improvements they suggest. If you do so, you will very likely see your improvement efforts bloom! If they see you are truly interested in their ideas and are willing to allow them the time and materials needed to change the small things that bug them regularly, you will be surprised how much this will mean to them. And your business will benefit at the same time.
This may sound simple but if you ask, you must also be prepared to offer support and provide time and resources to allow them to make the improvements they suggest. If you do so, you will very likely see your improvement efforts bloom! If they see you are truly interested in their ideas and are willing to allow them the time and materials needed to change the small things that bug them regularly, you will be surprised how much this will mean to them. And your business will benefit at the same time.
Lean Tip #550 - Participate in an improvement project team meeting, training session or kaizen event at least once per month.
Be a visible, active participant in lean training and improvement efforts. If a manager makes time to participate or attend, it sends the message to employees that the activity is important. The opposite is also true.
Be a visible, active participant in lean training and improvement efforts. If a manager makes time to participate or attend, it sends the message to employees that the activity is important. The opposite is also true.
Lean Tip #551 - Ask to be shown an implemented improvement idea from all areas reporting to you at least once per month.
Recognition is an important component of all good Lean programs. When you take the time to "go see" some of the ideas that people have implemented and, better yet, thank them in person for a job well done, you are recognizing and reinforcing desired behaviors. You'll also get an important opportunity to learn more about both your employees and your processes. And when you ask to see improvements you are also setting the expectation that there will be some!
Recognition is an important component of all good Lean programs. When you take the time to "go see" some of the ideas that people have implemented and, better yet, thank them in person for a job well done, you are recognizing and reinforcing desired behaviors. You'll also get an important opportunity to learn more about both your employees and your processes. And when you ask to see improvements you are also setting the expectation that there will be some!
Lean Tip #552 - Read at least one new lean article or book a month.
Lean managers recognize that learning is a life-long endeavor that needs to become as natural to employees as breathing. The idea behind reading on lean subjects is to become a sponge, soaking up what others who have been on the journey longer than you have learned, and then think hard about how you and your organization can use this knowledge. Don't be surprised if you begin to accumulate your own lean library very quickly once you commit to becoming a reader!
Lean managers recognize that learning is a life-long endeavor that needs to become as natural to employees as breathing. The idea behind reading on lean subjects is to become a sponge, soaking up what others who have been on the journey longer than you have learned, and then think hard about how you and your organization can use this knowledge. Don't be surprised if you begin to accumulate your own lean library very quickly once you commit to becoming a reader!
Lean Tip #553 - Attend a conference, plant tour or participate in a webinar or podcast on lean topics once per quarter.
Better yet, take a few people along for the ride when you participate in these activities. Networking, benchmarking, and seeing and hearing about experiences of other companies and people are not only desirable but are expected in the world of lean practitioners. When a team of people from your company participates together you instantly increase the likelihood that the learning will be more widely shared upon your return and you create a unique way to foster team work and stimulate lean dialogue.
Better yet, take a few people along for the ride when you participate in these activities. Networking, benchmarking, and seeing and hearing about experiences of other companies and people are not only desirable but are expected in the world of lean practitioners. When a team of people from your company participates together you instantly increase the likelihood that the learning will be more widely shared upon your return and you create a unique way to foster team work and stimulate lean dialogue.
Lean Tip #554 - Visit at least one external customer or supplier each quarter.
The value stream does not stop at your four walls. Instead it extends both to your suppliers on the one end of the value chain and to the customers who pay the bills on the other end. The more you know and understand about these key stakeholders, and vice versa, the greater the chances that you can improve your extended value stream.
The value stream does not stop at your four walls. Instead it extends both to your suppliers on the one end of the value chain and to the customers who pay the bills on the other end. The more you know and understand about these key stakeholders, and vice versa, the greater the chances that you can improve your extended value stream.
Lean Tip #555 - Develop your own "Manager's Standardized Work".
How many of you have a written routine that you follow as you go about your daily work? I imagine if I asked you to list what you do, you would be able to list many things that have to get done in the course of the day, week or month. Why not formalize your list and establish your own set of manager's standardized work? It will help you and the people who work for you more than you know. Write down, in the sequence you will follow, indicating how much time will be devoted to each task and when it will be done each day, the repeatable activities you will undertake on a daily basis, a weekly basis and so forth. It is ok to reserve times for the "unknown" things that invariably come up. After a few weeks of practice you will have a pretty good sense of how much time you need to hold aside for these activities.
How many of you have a written routine that you follow as you go about your daily work? I imagine if I asked you to list what you do, you would be able to list many things that have to get done in the course of the day, week or month. Why not formalize your list and establish your own set of manager's standardized work? It will help you and the people who work for you more than you know. Write down, in the sequence you will follow, indicating how much time will be devoted to each task and when it will be done each day, the repeatable activities you will undertake on a daily basis, a weekly basis and so forth. It is ok to reserve times for the "unknown" things that invariably come up. After a few weeks of practice you will have a pretty good sense of how much time you need to hold aside for these activities.

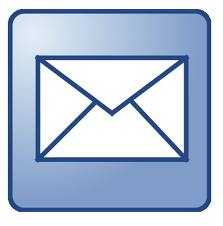





Love the Lean Tips! Sometime one comes along right when I need it. Thanks!
ReplyDelete