Company safety policies generally have two important objectives. First, safety policies aim to ensure a company's compliance with federal, state, and local laws and, therefore, to avoid fines and other forms of punishment for violations. Second, and more importantly, these policies strive to prevent accidents and injuries in the workplace so that employees remain healthy.
Since lean business philosophy gained traction, some critics have charged that a strict focus on lean initiatives compromises a company's ability to deliver on these goals of complying with the law and keeping workers safe. Lean detractors reason that a focus on efficiency, productivity, and avoiding waste could diminish concern for employee safety, thus putting workers at risk.
Extensive research and the experience of many lean proponents around the globe have cast serious doubt on those unfounded theories. In fact, companies that adopt lean strategies generally report enhanced workplace safety and reduced on-the-job accidents and injuries. The information below reinforces the idea that a keen emphasis on preventive safety measures is, in fact, compatible with lean business philosophy.
The Bottom Line: Workplace Injuries are the Epitome of Waste
One of the lean movement's primary goals is to eliminate waste (whether it be wasted time, wasted resources, or wasted money). An unsafe workplace is a breeding ground for waste. Indeed, an employee injury leads into a waste explosion!
First, production must stop so management can survey the scene and take action to care for the worker's injuries. A halt in production is wasted time. Let's assume the employee has a great deal of experience, and his absence from work means a less skilled replacement must take over. That worker's diminished skill level will likely lead to less productivity. Then, if OSHA investigates, the facility inspection will likely create a further disruption to the normal orderly operation of the company's business.
If this cycle continues, where employees suffer injuries routinely, insurance rates will rise. In addition, chances are that employees who observe the accidents and their supervisors will become witnesses in workers' compensation litigation, creating a further drain on progress. In short, lean leaders have a vested interest in promoting safety in the workplace.
Preventive Safety Measures are Compatible with Lean Philosophy
In many ways, the interests of safety gurus and champions of all things lean are consistent. Take ergonomics, for example. Studies show movements that incorporate poor ergonomics typically take longer than motions with good ergonomics. And, as we all know, poor ergonomics can lead to a wide range of physical ailments. Therefore, managers should instruct workers on the safest (and, in many cases, the fastest) movements to employ when carrying out their duties. These movements and methods will then become standard practice, thus reducing unnecessary repetitive motion injuries and increasing productivity.
Pay Attention to Details
Lean principles can provide innovative solutions to what might appear to be insignificant, though wasteful and harmful, business practices. Consider an employee whose daily routine involves lugging heavy boxes from one place to another. Even if supervisors have instructed him on the safest way to lift heavy items, the constant strain could eventually lead to injury. The brilliant solution? A hand truck or dolly. No, it's not rocket science, but minor adjustments like that can make the difference between a healthy worker and a former employee on disability. In addition, now the worker can push several boxes at one time and complete his tasks much more efficiently.
Apply Safety Principles to Get Lean Results
The preferred order of dealing with recognized hazards is:
- Use engineering controls to eliminate the hazard.
- Institute administrative controls to deal with the hazard.
- Use protective equipment.
Look at the previous example of carrying heavy boxes as a recognized hazard of repeated back strain. The least effective control is to provide a back brace, because that requires the worker to wear it every time. An administrative control would be to teach proper lifting technique. Eliminating the hazard by providing a hand truck is safer and more efficient. But what would happen to efficiency if you took the engineering control one step further and designed the process so the boxes were stored right where they are most needed?
Don't Underestimate the Importance of Staff Morale
If employees suspect that management is not concerned with their safety, animus will ensue. Dissatisfied workers become uncooperative workers. Uncooperative workers are often vocal, and their attitudes can impact the environment of the entire facility. Productivity will undoubtedly suffer. In contrast, employees who have a sense that their supervisors respect them and have a vested interest in their wellbeing will often return the favor. Satisfied workers become cooperative workers. Cooperative workers are typically efficient, productive, and don't cause problems.
Although lean proponents and safety experts may initially come to the table with different goals in mind, their objectives are not inconsistent. By implementing preventive safety measures in the workplace, companies often recognize unintended results that reflect the values of the lean movement. While going too lean could conceivably compromise workplace safety, smart decisions and careful planning can easily ensure a healthy balance.
About the Author:
Jay Acker is the leader of a Safety Services production team. Jay leads a team who supply businesses with regularly updated OSHA compliance related materials and a range of services for workplace safety. At www.safetyservicescompany.com, Jay Acker's editorial group makes materials for conducting weekly safety meetings, safety training programs, posters and other items.

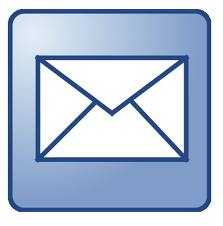





No comments:
Post a Comment