FMEA is a systematic analysis of potential failure modes aimed at preventing failures. This is intended to be a preventative action process carried out before implementing new or changes in products or processes. An effective FMEA identifies corrective actions required to prevent failures from reaching the customer and to assure the highest possible yield, quality and reliability.
What Is An FMEA?
- A tool used to evaluate potential failure modes and their causes.
- Prioritizes Potential Failures according to their Risk and drives actions to eliminate or reduce their likelihood of occurrence.
- Provides a discipline/methodology for documenting this analysis for future use and continuous process improvement.
Analytical technique used by manufacturing / engineering team as a means to assure that, to the extent possible, potential failure modes and their associated causes or mechanisms have been considered and addressed. This systematic approach parallels and formalizes the mental discipline that an engineer goes through in any manufacturing planning process.
Process FMEA Benefits
- Identifies potential “manufacturing or assembly” process failure modes.
- Identifies potential “product related” process failure modes.
- Assesses the potential customer effects of the failures.
- Identifies operator safety concerns.
- Identifies process variables on which to focus controls for occurrence reduction / elimination or detection of the failure conditions.
- Develops a ranked list of potential failure modes ranked according to their affect on the customer, (both external & internal), thus establishing a priority system for corrective actions.
- Feeds information on design changes required and manufacturing feasibility back to the design community.
- A list of potential process failure modes.
- A list of processes or process actions to:
- reduce Severity
- eliminate the Causes of product failure modes
- reduce their rate of Occurrence
- improve product defect detection if process capability cannot be improved.
- A list of critical characteristics and special controls to be entered on a Manufacturing Control Plan.
FMEA Facilitators:
- Experienced in methodology, guides PFMEA
- Does all the grunt work, finds and gathers all the data
- Subject matter experts
- Gives opinions and estimates, data if available
- Guides facilitator to source of data if not immediately available
- Verifies what Facilitator writes down
- Increases the probability that potential failure modes and their effects have been considered in a cross-functional team environment.
- Aids in the planning or development of processes and testing
- Ranks potential failure modes according to the effect on the customer, hence prioritizes improvements and controls for best use of limited resources
- Sets priorities for manufacturing controls
- Proactive concurrent engineering & manufacturing approach

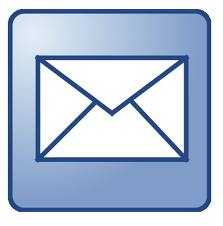





A key point of PFMEA is keeping it as a living document. You have to update it frequently or whenever you found a problem with process.
ReplyDelete