The first step in eliminating waste from New Product Development (NPD), and thus improving the process, is to learn to identify the eight wastes. By closely examining the entire NPD process from a Lean perspective, the opportunities to drive out waste and increase value will become obvious.
Defects
Defects are the result of executed processes that did not produce value.
• Improper information on drawing
• Missing views on drawing
• Incomplete information
• Product flaws resulting in missing customer expectations
• Reworking product or processes
Overproduction
Waste from producing product that is not currently needed or product that is not needed at all.
• Unnecessary documentation
• Cost overruns due to excessive project time charging
• Overlap of strategic and non-strategic projects competing for limited resources
Waiting
No value is added while people wait for product to process or product waits for people or machines.
• Unbalanced workflow within the team
• Time spent getting approvals
• Dependant on the number of hand offs and task dependencies
Non-utilized resources/talent
The waste of underutilized intelligence and intellect commonly referred to as behavioral waste.
• Underutilizing people’s knowledge and creativity
• Uneven work flow resulting with some team members overburdened while other underutilized
Transportation
While the product is moving, no value is added to it.
• Carrying, mailing, or even e-mailing documents stops the process
• In an electronic system look at the number of hand offs where we pass something to someone else
Inventory
Inventory is the collection of unprocessed documents, data objects, and transactions queued-up between people and processes.
• Drawings and specification - we invest time to make them, update them, and manage them
• Collections of unprocessed information and data
Motion
Excess movement by people or equipment only consumes time and resources without producing value.
• Efficiency of software – number of mouse clicks, number of routines, number of transactions
• Frequently searching for drawings and other information on remote shared services like servers or printers
Excess Processing
Doing more than what is necessary to generate satisfactory value as defined by the customer.
• Using software that has a function beyond what is needed
• Product designs or processes that are too complex
• Unnecessary steps in design process
• Excessive number of iterations
• Over-designed or over-engineered product
The acronym I prefer for remembering the eight wastes is DOWNTIME since it symbolizes lost opportunity. Another one that works well for NPD is TOWISDOM where S is skills. NPD is one essential element in the growth strategy that is so critical in all companies practicing Lean Thinking.

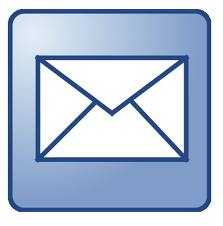





Nice summary. We often don’t take the time to analyze what we are doing, and wonder why the results don’t change.
ReplyDeleteThat is the key. Learning to see is the first part of continuous improvement.
Delete