Operator
error is often used in corrective action as a cause of failure. Although
operators can make errors, operator error is not an acceptable cause of failure
because it is not actionable. It is very often overused by the lazy or those
who don't know any better but human error can almost always be mitigated.
Processes
must be designed to expect that operators wish to do the correct thing.
Training and providing work instructions and procedures are not robust enough for
repetitive processes. Poor training and / or work instructions are inadequate
secondary choices to operator error. The real issue is the operator discovers
errors made in the process design. The process designer / engineer must strive
to engage operators into the process and help reduce the number of possible
errors available for operators to find.
We
must approach operator error by considering the interfaces of the process that
the operator is engaged in. The process should be designed to permit
communication between the process and the operator.
With
the process interface in mind, we must ask why one more time to cascade from
operator error, down to specific actionable topics. Here are some examples of
these actionable topics:
Actionable Topics to Replace "Operator Error"
Work
Station Design
- Bench/Table Height
- Organization of work tools (5S)
- # of tools and placement
- Component Positions
- Quantity
- Similarity
- Extended Reach (occasional)
- Lighting
- Comfort Features
- Foot rests/seat position
- Standing work bench position
Ergonomics
- Height and Reach
- Work type
- Weight
- Lifting
- Motion
- #of steps
- Degrees of freedom
- Work station interface
- Blind operation
- Posture
- Insertion force
- Static insertions
- Plastic deformation of end
source
- Tool
- Vibration
- Tool design
Documentation
and Training
- Illustrations Process
Documentation
- “A4” One page
- No Documentation
- Validation of Standard Work
Practices
- Testing
- Demonstration
- Frequency of validation
- Training
- Definition
- Measurement of Success
- Complexity of documentation
- Labeling
- Legibility of work instructions
- # of pages
- Understandability (5 second
rule)
- Fonts size and type
Assists
and Tool Design
- Error proofing features (lack of)
- Tool calibration
- Pallet compliance
- Correct tool
- Multiple look alike
- Life of tool
- Wear out
- Fixture control
- Maintenance
- Clamp pressure
- Inadequate
- Too great
- Cycle completion/interruption
- Locators / proximity sensors
- Life expectancy
- Measurement instrument
degradation
- Environment
Cognitive
Attention and Concentration
- Audible Noise (Interruption)
- Environment
- Temperature
- Humidity
- Sensitivity to Interruption
- Repetition
- Motion
- Trance/Zone Inducement
- Sound Quality
- Harmonics
- Vibration/cyclical noise
Processes
designed with operators in mind provide feedback to the process status. This
process interface can be passive or active. Passive interfaces use visual cues,
such as seeing parts remaining in a kitted bin or tactile feedback when
installing a part or engaging a clamp. Active interfaces use logic, sounds,
lights, process interruption or lockouts as feedback. Ultimately, Poka Yoke (error
and mistake proofing) are deployed in order to eliminate or reduce errors
discovered by operators.
Operator
error is not actionable but the causes of operator error can be addressed by
process and product changes. Don’t take the easy way out and blame the
operator. Ask why, and then improve the process. Show Respect for People.

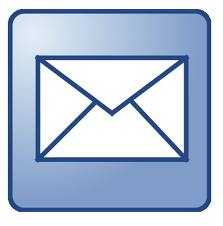





If you answer is that a person was at fault, I would even ask why several more times. Another question to ask is why were they allowed to do so? Why was it so easy for them to do so (if it was)? Can't we design the process to make the error much more difficult or impossible? Sometimes the process needs to leave the operator with the potential to easily mess up.
ReplyDeleteOperating on the wrong leg or arm, is inexcusable (processes can make this essentially impossible). Having the sharp scalpel with freedom of movement that lets a surgen cut something that causes a problem might well be a situation that has to exist in order to allow them to do what is needed. They probably need to be able to have dangerous sharp items to do what is needed, we can do things to make the environment safer but the process can't eliminate all risk (as far as I can imagine) in some cases.