On ASQ’s Blog, President Paul Borawksi asks if you are willing to take risk to find solutions to quality challenges:
And, I want to know how you—the quality professional–handle failure in the workplace. Do you try again until you find a solution? Are you penalized for failure? Or do you avoid it altogether? How much risk are you willing to take to find solutions to quality challenges?
To
err is completely human, so you should not be afraid of the mistakes you may
make and of course, you should never hide them. Nobody likes to make mistakes.
However, the simple reality of life is that at some point, all of us are going
to be wrong. That’s just life. We are going to make mistakes.
Treat
every mistake as an opportunity to learn and grow. Don’t feel stupid or doomed
forever just because you failed at something. You can always find other
opportunities.
A
colleague of mine always said, “Learn to fail quickly.” Essentially, if you are
going to fail you need to learn to do it quickly in order to get the data
(results) that you can use to gradually improve. The faster you get at learning
from unforeseen circumstances and outcomes, the faster you can find a solution
that truly adds value.
If
you’re not making mistakes, you’re not improving. Henry Ford said, “Failure is
merely an opportunity to begin again knowledgeably.” Failure can be an
inevitable stepping-stone to great achievement.
Fear
of failure is a genuinely scary thing for many people, and often the reason
that individuals do not attempt the things they would like to accomplish. But
the only true failure is failure to make the attempt. If you don't try, you
gain nothing, and life is too short a thing to waste.
But
to have success, management must create an environment where it is safe to
fail. Failure is an expected part of the process of finding solutions. If
workers feel that they have to “hit one out of the park” every time they come
up with an improvement idea, they will be reluctant to provide their ideas. In
a Lean environment, failure and success should be met with the same level of
enthusiasm and support.
As
a supervisor, you should work to create an environment where improvements are
encouraged and failures are embraced. An environment where ideas are
continually tested and then those that work are adopted. This cycle of
continually learning and improving is at the heart of Toyota’s success.
Management
needs to establish an environment where failure is acceptable. Failures can
either destroy or advance our goals, but it's our response to them that truly
determines the outcome. If we are too afraid of failure to try then we will
never know if we can improve our situation.
I’m part of the ASQ Influential Voices program. While I receive an honorarium from ASQ for my commitment, the thoughts and opinions expressed on my blog are my own.

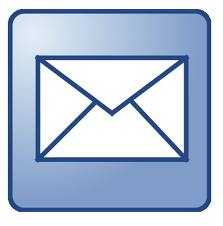




No comments:
Post a Comment