Click this link for A Lean Journey's Facebook Page Notes Feed.
Here is the next addition of tips from the Facebook page:
Lean
Tip #646 - Don’t Automatically Blame the Tool.
It’s
not the hammer’s fault if the person swinging it uses the wrong end. It just
won’t work well. Most tools are decent enough, they’re just used incorrectly.
Rushing to change a tool because things aren’t working well may be a mistake.
Lean
Tip #647 - Share More, Not Less When Implementing Process Improvements.
Even
in a small company, silos emerge. A policy of more sharing will help everyone
stay in touch with what others are doing, and create a collective expectation.
Keeping everyone pointed in the same direction is hard; sharing more about
what’s going on, how you’re doing things, reasoning behind decisions, etc. will
help.
Lean
Tip #648 - Identify Changing Requirements So You Don’t Lose Your Way.
Over
time your needs will change. You need to stay aware of this, so you can change
processes accordingly. Keep a list of your top requirements to help you make
better decisions on tools to use.
Lean
Tip #649 - Use Process Mapping to See the Entire Process.
Use
a whiteboard or large post-it note pads so everyone can see and think about
what starts the process. Then just keep asking the team, “and then what
happens,” until you get to the end of the process. The biggest challenge here
is making sure the team doesn’t go off on tangents. If you are leading, tell
the team that you are not solving any problems to start. You must understand
the process first before you look at ways to improve it. Process mapping allows
you to do this by seeing the entire process visually.
Lean
Tip #650 - Think Strategically On Your Process Improvements.
There
is nothing worse than optimizing a process and then having the entire system be
less than optimal. In order to understand the parts, you must understand the
whole. Get your entire team involved, understand the business strategy and
goals, and start thinking from a high level. After that you can drill down into
the details.
Lean
Tip #651 - Encourage Others: Give people something to prove.
People
grow when they have to prove themselves to themselves. Provide people and teams
with stretch assignments that hold them accountable to a higher standard of
performance.
Lean
Tip #652 – Encourage Others: Reward Courageous behavior.
It
is not enough to reward successful outcomes. To signal to the workforce that
behaving courageously is truly valued, you also need to reward courageous
behavior, regardless of whether that behavior produced a successful outcome.
When workers take calculated risks, or even make forward-falling mistakes,
their behavior needs to be recognized and rewarded if you expect others to
extend themselves too.
Lean
Tip #653 - Be a fixer, not a victim.
When
you see a problem that you think “someone” should address, ask yourself if you
could be doing something about it. It’s easy to complain or point fingers – it
takes courage to be a part of the solution.
Lean
Tip #654 - Keep your focus on being effective.
Effectiveness
is doing things in a streamlined manner.
It’s about getting things done and eliminating delay. By keeping “effectiveness” as your standard,
you’ll access your courage more often.
Lean
Tip #655 - Do something, take action.
Give
it your best shot to overcome your fear, no matter what it is. Trying builds
your strength, or else, you become more fearful if you let your (irrational)
thoughts overcome you. Preparation almost always does the trick if you're
apprehensive. If you're armed with the right skills and information, it's easy to
give that daunting job a go.
Lean
Tip #656 – Problem Solving Tip: Identify and fix the right root causes.
Complicated
problems have multiple root causes, probably more than you can fix in a
reasonable amount of time. Don’t waste time or money on causes that are either
insignificant in impact or only peripheral causes of the problem you’re trying
to fix.
Lean
Tip #657 – Problem Solving Tip: Choose solutions that are effective—and
implement the solution completely.
Identifying
the right root causes is necessary, but unless you then implement a solution,
you still have a problem. Double-check to be sure your solution plan really
will eliminate the causes you’ve identified, and then execute the plan. It’s
easy to get distracted by other projects once you get to the implementation
phase and never finish.
Lean
Tip #658 – Problem Solving Tip: Reward prevention.
Although
it’s generally understood that it costs more to deal with crises than to
prevent them, many companies do not recognize and reward those who push past
the symptoms to the root causes, preventing future occurrences. If you want to
focus on prevention, be sure to reward those who do it successfully.
Lean
Tip #659 – Problem Solving Tip: Everything necessary, nothing extraneous.
Make
sure you solve the problem completely, but don’t get sidetracked into doing
other things that won’t make this problem go away. Put those extras aside to
evaluate later as special projects.
Lean
Tip #660 – Problem Solving Tip: Everyone necessary, no one extraneous.
Make
sure everybody who can contribute to the problem solving effort is
appropriately involved. Only have the people on your team who will contribute
actively to solving the problem. People who need to know what’s going on can be
informed more efficiently in other ways.

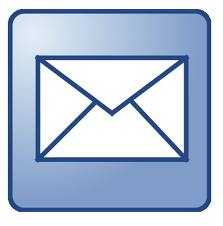





No comments:
Post a Comment