"Sometimes the best kaizen is no kaizen at all." — Jon Miller, Kaizen Institute
An
essential element in Lean thinking is Kaizen.
Kaizen is the Japanese word for continuous improvement or change for the
better. As no process can ever be
declared perfect, there is always room for improvement. Kaizen involves building on gains by continuing
experimentation and innovation.
Many
think Kaizen is about some sort of 5 day event where you shut down and make
improvement. Maybe this idea is fed by
consultants in some manner but Kaizen in fact is not this. It is about small incremental change, the
type of change that makes it easier to do your job. A change in which the people doing the task
are intimately involved in the improvement.
Kaizen
involves every employee - from upper management to operators. Everyone is
encouraged to come up with small improvement suggestions on a regular basis.
This is not a once a month or once a year activity. It is continuous.
Real
Kaizen thinking is based on making these little changes on a regular basis:
always improving productivity, safety and effectiveness while reducing
waste. The western philosophy is often
summarized as, "if it ain't broke, don't fix it." However, the Kaizen
philosophy is to "do it better, make it better, improve it even if it
isn't broken, because if we don't, we can't compete with those who do."

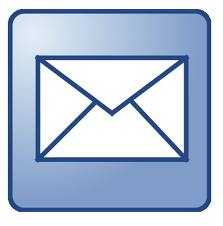





No comments:
Post a Comment