In
some organizations, we might as well give the quality folks a uniform, a badge
and a gun. They act like they are the Quality Police. Progressive companies
realize you cannot inspect quality into a product. By the time product is inspected, its level
of quality has already been established. The primary means of ensuring a
quality product is delivered is not by waiting until the product is assembled
to test it. Great companies build quality in from the start and maintain that
quality throughout the manufacturing process. To improve quality, you have to
improve the process that produced it.
Generally
the most effective way to achieve quality is to avoid having defects in the
first place. It is much less costly to prevent a problem from ever happening
than it is to find and correct the problem after it has occurred. Focusing on prevention
activities whose purpose is to reduce the number of defects is better.
Companies employ many techniques to prevent defects for example statistical
process control, quality engineering, training, and a variety of tools from the
Lean and Six Sigma tool kit.
Start
with the idea of preventing defects, not waiting until they are identified and
correcting them. Many companies have an active Zero Defects policy where defect
prevention is paramount and quality inspection is almost just a verification of
what they already know – that the product is defect free. If we can start with
quality and maintain that quality throughout the process we will have a quality
product.
Quality
must go beyond our product specification or contracted service. We cannot add
it at the end of the line or inspect it into the product. At best that is only
a false sense of security. If we want a quality product it must be made with
quality processes by quality minded people. A focus on quality must be
intrinsic to the company culture and practices for the customer to take notice.

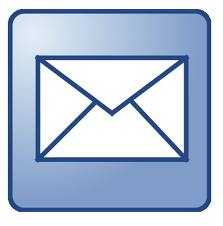





No comments:
Post a Comment