Yesterday,
I got a chance to get out the office and partake in EASTEC. The Society of
Manufacturing Engineers (SME) organizes EASTEC, one of the largest manufacturingshows on the East Coast highlighting the latest technologies and management strategies
for operational excellence. The theme
this year was “Human Ingenuity” meaning to envision a new product, it takes
human ingenuity. This was a great opportunity to see some old friends and
listen to a couple of Lean presentations.
I thought I would share some of my thoughts and learning from this event
with all of you.
First
up was Bruce Hamilton, from Old Lean Dude Blog and GBMP, to Lean Manufacturing
Plateaus. Since the mid-1990's many US manufacturers have benefited from
implementation of Lean manufacturing methods. Most of these implementations,
however, have plateaued far below their potentials, producing only modest and
sometimes transient gains, and failing to capture the passion and engagement of
true Lean transformations.
Bruce
says companies naturally plateau because they get too happy too soon. The earliest plateau occurs after some
initial stability from attacking low hanging fruit. In actuality if you are
focused on developing people it is all low hanging fruit. These plateaus along
the journey to true north can be counteracted by not only teaching the know-how
but teaching the know-why.
Plateaus
are going to happen and management must anticipate them. They are a temporary place to solidify
concepts and learning. Leaders must take the next step to move past their
comfort zone. It is management kaizen that gets you past plateaus. Companies
who break through realize that employee development leads to business (and
Lean) success.
Next
on the agenda was Ron Pujalte, a Lean Consultant from GBMP, who discussed How
to Leverage the Power of the Lean Triangle. For those who are not familiar with
the Lean Triangle it is made up of Philosophy, Technical, and Management factors
at the center of Human Development. Strategy must come before Philosophy.
Management must lead with commitment from everyone. On the technical side, tools are the means,
not the ends.
The
3 sides of the Lean triangle make a unique contribution to the overall triangle.
The component parts work together to encourage a strong culture that centers on
customers, leverages employee knowledge and creativity and continues to drive
organizational experimentation and learning year over year. Systems run the
business but it is people who the system. Management must provide the means of
connecting the dots. True North is always on the horizon. Getting there is the challenge.
Finally
good friend Tony Manos, from 5S Supply and sponsor here, gave a presentation titled
A3 Problem Solving Deep Dive. Many organizations are using the A3 methodology
to help solve problems and create better target conditions. The A3 is a way of
simplifying and filtering information to an 11x17 sheet. The form itself is not
a solution; it is the thinking and process that brings results. It is a working
document that is best done with a pencil and eraser than digital formats.
The
basic structure of the A3 follows the PDCA methodology which encourages Kaizen
(small experimentation continuously checking your hypothesis) that leads
developing people. The A3 is really about your personal learning and growth. It
provides great coaching moments along the process. To be effective people need
to know some basic problem solving tools before using an A3. A3’s are effective
and efficient closed looped system of problem solving.
EASTEC
proved to be another success for me. I was able to see many of manufacturing’s
greatest innovations on display first hand. There was an opportunity to network
with many leaders, practitioners, developers, manufacturers, and consultants in
my area. And of course I had the opportunity to learn from a number of great
Lean Leaders. Hopefully, you can take advantage of similar activities in your
area and share the learning as I have.

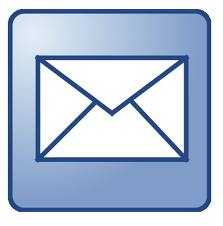





No comments:
Post a Comment