Click this link for A Lean Journey's Facebook Page Notes Feed.
Here is the next addition of tips from the Facebook page:
Lean
Tip #706 – Recognizing the Commitment of People Can Support Lean Adoption
You
need to start creating new stories in your organization to replace the old
ones. One of the best ways of achieving this is to recognize the commitment of
people who have really bought into the concept of Lean. That mean identifying
people who have done things that support the adoption of Lean and then telling
others what they did.
Lean
Tip #707 – The Power of ‘Thank You’ and ‘Well Done’
It
is impossible to underestimate the power of the phrases ‘thank you’ and ‘well
done’ when said with conviction to someone who deserves it. It recognizes that
the individual has contributed something of value and also helps to motivate
them for further participation.
Lean
Tip #708 – Create a Continuous Process Flow to Bring Problems to the Surface.
The
idea of flow is to reduce the time that any piece of work, person, or
project spends travelling between stages
in the process, or waiting for the next stage in the process to start. The
ultimate aim is to reduce this wait time and travel distance to zero.
Lean
Tip #709 – Use Visual Controls So No Problems are Hidden
As
human beings we react well to visual signals. The aim of this principle is to
make the performance of teams visible so that people can see what is going on.
This will enable them to see how the changes they make impact the team’s
performance.
Lean
Tip #710 – Become a Learning Organization Through Relentless Reflection and Continuous Improvement
Nothing
is perfect and everything can be improved. We must continuously review how and
what we do in order to find better ways of doing it. This means accepting the
occasional mistake and having the courage to admit it, along with the strength
of mind to find a better way of doing things in the future.
Lean
Tip #711 - Find the Middle Ground Between Fear and Comfort
Fear
is going to cause a lot of stress and it may even lead to dissent among
employees. On the other hand, comfort can lead to decrease in production. Lean
leaders must learn to eliminate these two scenarios or at least find the middle
ground between them.
Lean
Tip #712 – Lean Leaders Must Both Lead and Teach Employees
Many
leaders forget the teaching aspect of the role. To become an effective leader,
one needs to be able to teach. This is especially necessary when there change
is implemented and when there are new techniques and business strategies to be
learned. Leaders should not just be experts, instead they should be a resource
where employees can go to for assistance.
Lean
Tip #713 – Lean Leaders Meet Face-to-Face With Employees Regularly.
Face-to-face
communication continues to be the most effective. It allows people to hear you
talk. It should also give them an opportunity to ask questions, seek
clarification and share opinions with you. In other words, to ensure your
face-to-face communication is effective, make it two-way.
Lean
Tip #714 – Lean Leaders Encourage
People to Make Contributions
Let
the members of your team know that you welcome their ideas and expect it.
Leaders who encourage involvement from the group find this leads to greater
commitment, more creative problem-solving and improved productivity.
Lean
Tip #715 – Lean Leaders Build on Employees Strengths.
Everyone
focuses on improving weaknesses. However, you can find success by paying
particular attention to areas of strength. This builds confidence in your team
members and recognizes their contribution. You’ll find this rewarding for you
and your team members.
Lean
Tip #716 - Choose Where to Focus Your Improvement Efforts.
Leaders
are critical in setting an agenda for change. Identify the processes you
believe are high priority for improvement. Solicit input from staff and
customers to identify processes that are in need of attention and to assess
where there is the greatest potential for improvements. The processes selected as
targets for improvement efforts should be strategic priorities and/or those for
which you feel a “sense of urgency” for improving.
Lean
Tip #717 – Leadership Must Articulate a Vision and Goals Describing What They Believe
an Excellent Process Should Accomplish.
Provide
a clear charge to all layers of management and process improvement team members
to work towards this vision, making sure that everyone understands the vision.
Work with Lean leaders to set specific goals and a manageable scope for each Lean
event. Focus on defining the attributes needed for success and empower the team
to develop efficient and effective approaches to accomplish them.
Lean
Tip #718 – Leaders Need to Actively Participate in Process Improvement Events.
The
involvement and passionate commitment of leaders and senior managers is the
most important factor in the long-term success of process improvement efforts.
Attend process improvement events in their entirety, and invite additional senior
leaders to the report-out presentations. Encourage staff to elevate issues that
need resolution, and address those issues promptly. Ensure that all
participants in Lean events, including delegates of senior managers, are
empowered to make decisions and commitments during the events.
Lean
Tip #719 – Management Should Provide Visible Support for Process Improvement Efforts.
Make
it clear to people in your organization that you strongly support process
improvement efforts, both verbally and through your actions. Following an
improvement event, lead by example and implement the new process yourself.
Actively participate in follow-up meetings after the event, such as 30-, 60-,
and 90-day follow-up meetings, recognizing the team’s progress and reinforcing
the importance of continued implementation. Communicate in writing and in
meetings why it is important that everyone in the organization commits to
supporting and using the new process.
Lean
Tip #720 - Clear Obstacles to Successful Implementation.
As
new issues and challenges emerge, it is easy to lose focus on the performance
and improvement of existing processes. Create time to discuss performance of
work processes targeted by improvement efforts (and not just the issue or
crisis of the day). Routinely walk around the office/factory to check in with
employees at their work stations and ask specific questions about how the
process is working, what support is needed, and what challenges are being
experienced. Work to remove barriers. Where barriers cannot be removed, work
with managers to calibrate goals and strategies to optimize results.

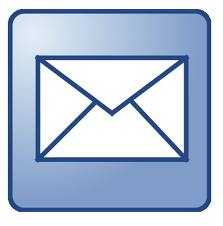





No comments:
Post a Comment