When
you ask a number of people to explain Lean Manufacturing in one sentence, most
of them will answer: “eliminate waste”. The reason is that eliminating waste,
or Muda is a relatively easy way of identifying the low hanging fruits for
improvement in an organization. However, Muda is not the only ‘M’ Toyota has
built its famous Toyota Production System around, there are two more: Mura
(Variation) and Muri (Overburden).
Muda,
in lean thinking, is defined as: all activities that do not add value from a
customer perspective and that can be removed.
Mura
is any variation leading to unbalanced situations. In short: unevenness,
inconsistent, irregular. Mura exists when workflow is out of balance and
workload is inconsistent and not incompliance with the standard.
Muri
occurs whenever people or equipment are being overburdened or overstressed. Any
activity asking unreasonable stress or effort from personnel, material or
equipment creates waste.
The
three M’s, Muda Mura and Muri are influenced by each other. Most organizations
only focus on eliminating Muda because they can be found by using a number of
tools, but also by close observations, but in Lean, if we want to take step to
eliminate wastes, the order should be:
1.
Mura: We have to first set up a system with no Mura, therefore, when we set up
the processes, they are all following a standard Takt time, and the capacity of
all the processes must first achieve a reasonable level of evenness by capacity
and takt time,
2.
Muri: When Mura is in place, Muri will quickly surfaced, there are areas where
Muri can occurred beyond the consideration of Mura such as high defect ratio,
bottle necking due to difficult operation,
3.
Muda: Once the Mura and Muri had been sorted out, then it will be time to
identify Muda in all the operations, material usage, defects etc.
Simply
wastes are not desirable, they need to be identified and eliminated, therefore
by knowing MUDA, MURA and MURI, the whole organization can take meaningful steps
to eliminate wastes and hence improving cost.
To
establish a lean process, the traditional system must be fundamentally changed
and the right process must be established. Once the new way of working has been
established, waste and variation must be systematically eliminated. The process
is hence incrementally and continuously improved. In sum, establish the right
process first by removing overburden. Then empower and encourage the teams to
eliminate waste and unnecessary variation relentlessly.

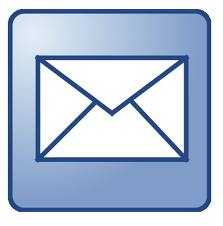





No comments:
Post a Comment