Despite the enormous popularity of Lean, the track record for successful implementation of the methodology is spotty at best. Some recent studies say that failure rates for Lean programs range between 50 percent and 95 percent.
A
Lean journey is full of steps not all of which are forward. Failure will occur.
Its ok, the purpose is learning, and we learn through experimentation. Trying
new approaches, exploring new methods and testing new ideas for improving the
various processes is exercise for the mind.
Restarting
the Lean journey can be difficult. It is critical to have alignment and clearly
state the need for improvement from the beginning. There are ten key steps that
should be taken when restarting the journey towards a Lean improvement.
1.
Establish a need to improve and obtain management commitment
2.
Define the improvement objective
3.
Identify and acquire necessary resources
4.
Collect information and determine current state
5.
Uncover the root cause
6.
Identify and test countermeasures that will meet the improvement objectives
7.
Develop plans for implementing the countermeasures which ensure buy-in
8.
Implement the improvement
9.
Standardize the improvement
10.
Repeat starting a step 1
Lean
implementation is not simple or easy. However, results show that, when done
properly, Lean lives up to its promises. Lean and its elements work. All of the
failure modes presented here can be avoided or overcome.
Lean
improvement is about the entire organization and everything it does. Lean
Thinking has to be a prime concern of executive management and its success
depends upon commitment from them. Their commitment must also be highly
visible. It is not enough to demand improvement. If executive management does
not demonstrate its commitment by doing what it says it will do they cannot
expect others to be committed either.
The
adoption of Lean is never a short or simple journey. A Lean transformation
takes time. It begins with understanding the core tenets of the Lean philosophy
and with focusing on the customer. It continues by incorporating the
methodology into the organization and involving every employee in developing a
refined work ethic. Overall, Lean is about adopting a lifestyle change—one that
requires an ongoing commitment to achieve organizational health and longevity.
If
you want Lean to succeed in your organization, management has to become a
student of Lean in order to be a successful sponsor. In other words, you have
to apply Lean to your management process first in order to understand how to
apply it to others.

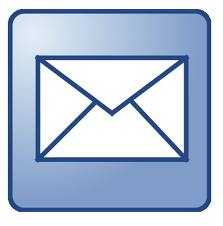





No comments:
Post a Comment