![]() |
fabufacture.co.uk |
One
of the most misunderstood aspects of Lean is the use of inventory. Inventory is one of
the eight deadly sins (wastes) in Lean manufacturing. This waste is often one
that hides other wastes in our businesses. I think most are familiar with the
river and boulder analogy. The water level in the river is the level of
inventory and the boulders in the river and the problems in our business. As we
lower the water level or inventory level those boulders or problems stick out.
It
is fairly well understood the financial impact of inventory. Certainly, in
these economic times it is not a surprise that many companies and their CEO’s
are focused on cash flow. Yet, well-intentioned efforts to reduce inventory,
more often than not, get only temporary results. Without effective business
process changes, the organization can easily slip back to old ways with
inventories (and costs) just climbing up again. I think question is should
inventory reduction be an objective of the business or a result of say
implementing improvements.
The
numbers on the company balance sheet do not tell the whole inventory story. The
overall inventory of an organization can be divided into 3 major groups: 1) Raw
material, WIP, and Finished Goods 2) MRO inventory (inventory of tools,
maintenance spares, misc. production items, etc.) and 3) Distribution inventory
(all materials in-transit of stored outside premises). Traditionally, inventory
reduction efforts have focused mainly on the first category. However, this
typically accounts for less than 40% of the overall inventory of a company.
One
of the major impediments to inventory reduction is the mistaken notion that
just improved inventory management is all that is required to get the job done.
The real culprits are the inefficient business processes that cause excessive
inventories to exist in the first place. It is often the case that the real
causes of excess inventory lie outside the purview of the supply chain
managers.
The
mantra here is that in order to get a bigger piece of the cake, one should
increase the size of the cake itself. So the objective should be one of
continuous improvement. We should consider improving production scheduling,
reducing cycle times, increasing manufacturing flexibility, improving quality,
improved forecasting, and developing and partnering with suppliers as the goal.
By addressing the cause of the increased inventory the gains can be sustained.
Reduced inventory quantities and dollars are then the resultant of said
improvements in the business system.
Lean
doesn’t mean ZERO inventory. It means the right inventory at the right time at
the right quantities and in the right place. Every company needs buffers, but
they must be well planned and controlled. As anybody who has spent some time in
a manufacturing plant will tell you, operating without buffers is a sure recipe
for disaster. Low inventories are commonly linked to Lean because many
organizations are able to reduce inventory levels due to practicing Lean
Thinking. But "true" Lean Thinkers understand lower inventories are a
resultant of a process improvement not a solution to a problem.
Keeping
the right amount of inventory is not straightforward, so managers need to
address the issue in a proper way. Management who do not truly understand Lean
teachings are often results orientated in our performance driven society. Inventory
decisions are risky and they make a large impact throughout the supply chain.
Without proper planning, a manufacturing company can run out of raw material,
negatively impacting the company and its customers. Likewise, overstocking of
raw materials, work in process inventory, or finished goods could also hurt the
company’s profitability.

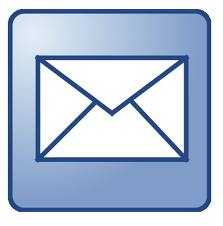





Inventory often misunderstood as a have or not have. In reality it should be well in between, and constantly striving for lower levels.
ReplyDeleteManagers in this process may come into weary waters, as problems can arise and their bosses might don't like to be accountable for that. So as a result inventory is increased once more just for the sake of quietness.
Leadership teaching managers not to fear such challenges is much more needed than the need for the "right" level of inventory.
just my 2 cents from plant experience
The very first lesson the TPS sensei taught us back in 1990 was REDUCE THE INVENTORY TO MAKE THE PROBLEMS APPEAR. We tried for years to solve global problems and find the "right" level of inventory - thus completely missing the point.
ReplyDelete1) the north star is ZERO INVENTORY (it's a star, we're unlikely to reach it any time soon;
2) put the inventory at THE RIGHT PLACE at the process that produced it
3) whatever your level of inventory, reduce it by at least 30%
4) solve problems as they appear 1 x 1
5) until you figure out what MISCONCEPTIONS generate the inventory in the first place: you are part of the problem :)
Lean guys, please get this - don't interpret JUST-IN-TIME in a way that makes it easier. Whatever your level of just-in-time, reduce lead-time. Dpn't rationalize, don't justify, control the lead-time, reduce the lead-time, solve the problems, teach people how to handle their problems and LEAN the process!!!!