My good friends at the Lean Enterprise Institute sent me Jim Womack’s newest book Gemba Walks Expanded 2nd Edition. In a significantly expanded second edition of his popular Gemba Walks book Jim Womack illustrates the power of rooting improvement efforts in deliberate visits to the “gemba,” a Japanese word for the place where value is created.
In
his first book Jim shared a decade of learning from Gemba Walks. He thought he
was done but that wouldn’t be Jim. He kept walking and learning. In 12 new
essays, ranging from the provocative to the practical Jim reflects on the past
30 years of lean, and assesses the current state of lean today.
The
new essays tell the origin of flow going back 100 years to Ford and the
discovery of Lean as told by those who were there to see it. To this he adds a
reflection on the last 25 years of Lean that while not perfect and easily fragile
has been a significant vehicle of innovation for the world’s managers. He
discusses Lean in other industry sectors like Government and Healthcare where
the challenges are no less demanding. Jim reviews shoring or as he calls it
Leanshoring as many companies return to the US.
Jim
reminds us that despite the growth of adoption of Lean Thinking (and in many
other industry sectors) there are still large amounts of waste. He challenges us to continue learning to see,
Gemba walking, and learning together.
I
am sure this will not be the last we hear from Jim and frankly I would be happy
with that. It is a pleasure to be able to learn from Jim Womack’s experience.
Gemba Walks Expanded 2nd Edition is eye opening, though provoking,
and completely informing. This is a must read for all business leaders at all
levels in all industries. Start your endless journey today by Gemba walking.
The
following was my previous endorsement of Jim’s first book on the subject Gemba
Walks from 2011.
Gemba Walks is Jim
Womack’s newest book from LEI. In Gemba Walks, Jim Womack a pioneer in bringing
Lean to the world, shares a decade of learning that will have a deep resonance
for both the Lean community and for anyone seriously engaged in improving any
value-creating activity.
The life of lean is
experiments. All authority for any sensei flows from experiments on the Gemba
[the place where work takes place], not from dogmatic interpretations of sacred
texts or the few degrees of separation from the founders of the movement. In
short, lean is not a religion but a daily practice of conducting experiments
and accumulating knowledge.
Over the past decade,
he has shared his thoughts and discoveries from these visits with the Lean
community through a monthly letter. In Gemba Walks, Womack has selected and
re-organized his key letters, as well as written new essays providing
additional context.
Gemba Walks shares
his insights on topics ranging from the application of specific tools, to the
role of management in sustaining lean, as well as the long-term prospects for
this fundamental new way of creating value.
The most productive
way to walk is to follow a single product family or product design or
customer-facing process from start to finish. As you do this you look at each
step with the eye of the customer and from the perspective of creating values
and asking how this can be done with less. This process Jim summarizes by the
phrase “Go see, ask why, show respect.”
In one of his newly
written sections Jim reflects on a decade of walking by sharing lessons he has
learned from all these Gemba Walks.
Lesson 1: The
critical importance of the simple act of walking. When you get bogged down,
distracted, or even discouraged rediscover the power of going to see.
Lesson 2: Never walk
alone. What is the benefit if only you see the current state and think of a
better way to create a future sate? Always walk the value stream with the
people who touch it. It will be their efforts who are needed to improve it.
Lesson 3: Expand your
focus. Many look primarily at the steps in the value stream and ask how to
remove the waste. You must ask about the support processes to get the right
people to the right place in the value stream at the right time with the right
knowledge, materials, and equipment.
Lesson 4: Reflect
first on the purpose of the process. Focus on what problem the customer is
trying to solve and ask whether the existing process, now matter how well, run,
can effectively address their problem. Pay special attention to the way people
are engaged in the operation and its improvement.
Lesson 5: Make work
fulfilling. There is nothing worse than seeing good people trapped in an
unfulfilling process that they lack the power to improve.
Lesson 6: Stability
before full panoply of lean techniques. The process must be capable (able to
produce good results every time) and available (able to operate when it is
needed).
As John Shook says in
the introduction Jim has a remarkable ability to frame issues in new ways,
asking why things are as they are, causing us to think differently. Something
he referred to as “intense noticing”. Jim inspired all of us by simply seeing
and communication lean best practices. He encouraged others to try new things
or to try old things in different ways. Offering others the courage to try
truly embodies showing respect for people.
I recommend Gemba
Walks to anyone serious about making improvements where humans create value.
Reading this book will reveal to readers a range of lean principles, as well as
the basis for the critical lean practice of: go see, ask why, and show respect.

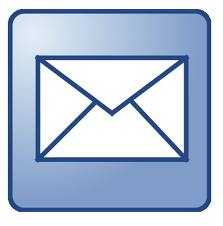





No comments:
Post a Comment