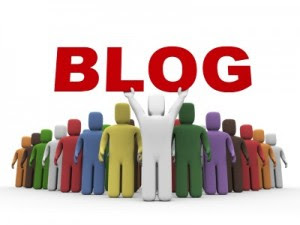
A
selection of highlighted blog posts from Lean bloggers from the month of April,
2014. You can also view the previous
monthly Lean Roundups here.
The Big
Kata – Michael Lombard discussed the benefit of having one single scalable
approach to improvement.
Look
Below The Waterline to Understand Lean – Hakan Forss says you need to look
past those things that are visible like tools and techniques to truly
understand Lean.
Make
Meetings Meaty, Mobile and Memorable – Liz Guthridge says there is value in
incorporating three elements into as many meetings as possible.
The Road to Lean
– Bruce Hamilton says when the road to Lean is paved with the wrong intentions;
it is destined to hit a dead end.
More
on Toyota's "Respect for Humanity" – Michel Baudin explains
Toyota’s “Respect for Humanity” from those who experienced it directly.
How
Do You Make Time for Improvement? Here are Nine Takes – Mark Graban
summarizes the feedback from 9 experts on making time for improvement.
Ask Art: How Do
We Prevent Backsliding? – Art Byrne explains the proactive steps that can
be taken to prevent backsliding on improvements.
How
Lean Improves Individual Productivity – Dan Markovitz shows how Lean can be
used to improve personal productivity.
Respect and Leadership
- You Can’t Have One Without The Other - Jacklyn Whitaker shares three tips
to improve your leadership skills by respecting your team members.
The Power of Hope in
Improvement – Karen Martin says that while need more than hope to get
results it is good place to start.
Quality
of Lean – Bob Emiliani says the quality of Lean in an organization is
driven largely by people being allowed by their leaders to think.
“Be Lean” vs. “Do
Lean” – Chad Walters says there is a difference between being Lean and
doing Lean as a corrective measures.
Value
Stream Mapping: Ferrari or Pinto? – Karen Martin explains 6 common mistakes
to avoid when value stream mapping to get the most benefit.
How
to Create a Dysfunctional Culture Where Employees & Customers Are Unhappy
– Mark Graban takes the what not to do approach to employee culture as a lesson
for all.
Sustaining
Lean – Bob Emiliani compares the decline of Scientific Management in 1908
to that of Lean Management today and what it takes to avoid it.
Bus Schedules and the
Lean Management System – Mark Hamel explains why mature Lean organization
maintain a profound and pervasive respect for schedules.
What Is
Respect For People? – Chad Walters shares his thoughts on respect for
people and what it means for organizations.
Working
outside in rather than inside out – Bill Waddell discusses supply chain
optimization from customer’ s view or the company’s view.
Productivity
Problem Solved – Bill Waddell shares four common productivity measurement
traps to avoid.
No Time for Kaizen? Check Your
Assumptions – Jon Miller says kaizen is part of the job and the CEO sets
the priorities.
This is honestly more about leadership
than lean – Art Smalley says that lake of time for improvement is
leadership problem.
Lean is the strategy! – Michael
Balle says that Lean leaders look for kaizen in the Gemba.

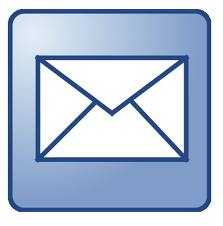





No comments:
Post a Comment