"An ounce of prevention is worth a pound of cure." — English Proverb
Generally
the most effective way to achieve quality is to avoid having defects in the
first place. It is much less costly to prevent a problem from ever happening than
it is to find and correct the problem after it has occurred. Focusing on
prevention activities whose purpose is to reduce the number of defects is
better. Companies employ many techniques to prevent defects for example
statistical process control, quality engineering, training, and a variety of
tools from the Lean and Six Sigma tool kit.
Start
with the idea of preventing defects, not waiting until they are identified and
correcting them. Many companies have an active Zero Defects policy where defect
prevention is paramount and quality inspection is almost just a verification of
what they already know – that the product is defect free. If we can start with
quality and maintain that quality throughout the process we will have a quality
product.
Quality
must go beyond our product specification or contracted service. We cannot add
it at the end of the line or inspect it into the product. At best that is only
a false sense of security. If we want a quality product it must be made with
quality processes by quality minded people. A focus on quality must be
intrinsic to the company culture and practices for the customer to take notice.
Quality
is about prevention—you cannot "inspect" quality into a product. It
has to happen before the inspection process.

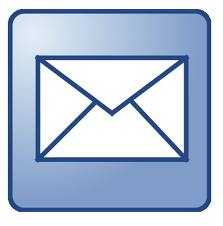





Great quote! Many quality engineers and managers are focused on defect detection vs prevention. I have seen so many companies with multiple layers of extra inspection. If these resources were focused on investigating the root cause, they could identify prevention methods and improve quality at the source.
ReplyDelete