Last week on The Lean Edge authors were asked
about the role of a sensei:
What is your experience of working with sensei,
and what advice should we give executives seeking to learn lean deeply
regarding senseis?
It
is a very good question so I wanted to share my thoughts on the matter.
Lean
manufacturing is a very broad philosophy for business improvement that has many
tools/techniques to aid you in making your production or service more efficient
and better at offering your customer a great value. Being able to successfully
implement Lean across a company is not something that you can pick up from
reading a few Lean implementation books, nor is it something that you can learn
from a training course in your local hotel, to truly be able to implement Lean
you have to have lived and breathed it for several years to gain enough
experience.
This
leadership role has many names. Whether
you call them a sensei, champion, coach, or leader; the role is no less
critical for the organization to be successful.
I am not one that pays much attention to titles but for this post I
chose Coach because it is so fitting. A
Coach is an individual involved in the direction, instruction and training of
the operations of a team or of individual.
The
following characteristics are desirable for a good Lean Coach:
- Active-learner open to new ideas
- Natural problem-solving skills
- Basics technical skills
(comfortable with spreadsheets, graphs, data, etc.)
- Keen Observer
- Hands-on
- Passionate about improving
processes
- Leadership skills
- Strong interpersonal skills
- Excellent communicator (writing
& speaking)
- Systems thinkers (able to
understand process flows, etc.)
These
characteristics alone don't make a Lean Coach.
The Lean Coach must have technical knowledge in the lean tools and tacit
knowledge from experience. Nobody is
born knowing these principles and how to implement them. Everyone has to learn them through practice,
trial and error, and coaching. Success
is not based on who you are but rather on what you do. Behaviors can be learned
and unlearned.
Being
a teacher is the most important aspect for a Lean Coach. They are not the ones to come in and do it
for you. They are the ones to show you
how to do it with confidence so that you will be able to do it for
yourself. A Lean Coach must be
relentless in teaching and expecting learning through actual practice.
The
focus of a Lean coach is to provide coaching on the principles and practices of
Lean Thinking to individuals and groups of employees within manufacturing and
service industries. A Lean coach can be advantage because of the following
reasons:
Knowledge
A
Lean coach brings a range of experiences from previous Implementations that can
help you to ensure that your implementation will be smooth and efficient. They
also have the experience of implementing the various lean tools in different
situations so they will understand how to involve your people and guide them in
achieving the best possible results. Most Lean coaches will also have people
and organizations that they can go to gain additional expert advice and help,
contacts in other industries and companies with whom you can share experiences
and view successes.
Perspective
A
Lean coach that is independent from your organization and not burdened by the
internal politics or any pre-conceived ideas of how the place should work has a
clear mind with a bias for action. They can challenge status quo and ask those
hard questions to get you out of your comfort zone and to think of those out-of-the-box
ideas you need.
Pressure
A
good Lean coach should be continuously pushing your company. They will be able
to focus on the specifics of the implementation and not be distracted by the
other things that may be going on within your company. A Lean coach can apply
the constant gentle pressure required for transformation to take hold.
Choosing
the right Lean coach to help you make the move from traditional manufacturing
to Lean manufacturing is very important. A successful Lean coach must have the
ability to convince people at all levels of the organization. No matter whether
you are using a Lean consultant or someone on staff, full company-wide support
is imperative in making the changes work. Management will have to fully support
the Lean coach in Lean projects, and employees will have to be convinced to
implement the changes wholeheartedly.

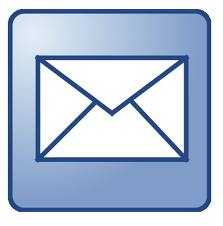





No comments:
Post a Comment