Here are some thoughts on how to facilitate an event.
1. Start small. Trying to do too much when introducing a new process can be overwhelming. Strive to accomplish small steps over time and build on your successes.
2. Expect to use extra time at first when planning to incorporate activities for reflection. Extra time spent in up-front planning will help reduce challenges during delivery of activities or in follow-up.
3. Work with a colleague whenever possible. You and your colleague can provide each other with a sounding board for ideas and mutual support.
4. Make a collection of activities and ideas. Evaluate the ones that work and those that do not. Revisit old activities occasionally; fresh eyes may see new opportunities for old ideas.
5. Be persistent. If you feel that the process is not working, reflect on the experience to gain new insights. Identify the issues, create solutions, and make necessary adaptations. As a facilitator, consider:
What worked?
What could have been better?
How did the students respond to the activity?
What feedback did colleagues give about the activity?
Was I open to honest feedback (or was I nervous about receiving constructive comments)?
What adaptations could be made to the activity?
How did I respond to the activity?
How could I adjust my approach to enhance the process?
6. Remember that expertise develops over time and often through a process of trial and error. See this learning process as a journey, rather than the destination.
As a Lean facilitator, if you apply these sensibly you will not go far wrong. Just remember to try it. It's easy to forget about these simple things during the heat of battle.

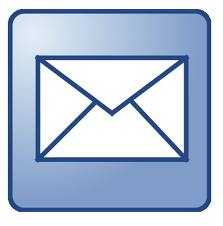





Great advice. All it takes is to start small, and learn from each step.
ReplyDeleteDoing a reflection right after each event with all participants (as short as possible) has become second nature. I learned it in Finland from a management school where there are no professors, up there it is called "Motorola" and we shaped it into "#PresencingStatus" putting answers to four short questions (What has been good? What has been tricky/unsatisfied? What have I learned? Next action?)
There will be always room for improvement.Building the trust amongst the project members (across the hierarchy) will raise with the number of events, and their positive impact on the processes the participants are involved.
Not a quick development - however worthwhile
h/t Johann Anders for letting me know via Google+ about this post
Excellent tips..I think each event will have different objectives and different requirements. These are the great ways while start leading or facilitating lean events, you have prepared with a great list of kit supplies to have during the event. Thanks for posting it.
ReplyDelete