Despite Lean Thinking be around for three decades there are still surprising many misconceptions about Lean. We often hear what the definition of Lean is but this time I wanted to share what Lean is not! Here is a list of 10 things Lean is not:
1.
Lean is Not about Tools
Tools
do not solve problem but rather people do. It is not about the tools it’s how
they are applied. A large number of organizations have failed to produce the
desired results from the direct and prescriptive application of Lean tools. The
tools themselves have been proven to work in many situations. The difference
must then be in how the tools were applied, their appropriateness, but not the
tools themselves.
2.
Lean is Not Devoid of Technology
The
fundamental principle of Lean manufacturing is to design a simple manufacturing
system, however, that does not mean eliminating technology. There is always
room for improvement.
3.
Lean is Not Only for Manufacturing
Whether
it is lean manufacturing, lean office, or lean management, benefits can be
realized throughout the company in inventory reduction, productivity
improvement, and reduction in errors, to name a few.
4.
Lean is Not about Waste Reduction
First
and foremost, Lean is about value — a bigger and more inclusive concept than
mere waste. Lean is a systematic way to learn to see the inefficiencies in your
processes and to solve these opportunities in such a way to grow the business
profitably by adding value the customer will pay for. If you want to be a
successful company you will learn to empower and engage the entire organization
to focus improvement on value-added work from the customer’s perspective.
5.
Lean is Not about Cost Reduction
Lean
is all about finding better ways to do things, so that they require less
effort, less time and fewer resources. It is not about cost reduction –
penny-pinching, cutting investment, taking out people – it is about finding
better ways to get work done. Traditional cost cutting occurs in silos, without regard to who is
affected upstream and downstream. These impacts cannot just negate the initial
cost reduction from the unilateral approach, but exceed them. Lean examines
each process, internal and external, finding and removing the waste, and
reducing cost while maintaining the health of all constituents.
6.
Lean is Not Only for the Frontline
Lean
is meant to involve the whole company. It is not intended to be put into action
in only one area. It is a management philosophy which should include every part
of your organization. This helps promote the concept that everyone in the
company is part of the team. True Lean manufacturing needs the involvement of
everyone coming into contact with the company’s product and its customer.
7.
Lean is Not about Less (or more with Less)
Lean
manufacturing is not a head-count reduction system; instead Lean manufacturers
understand employees on the shop floor know their work best. Lean manufacturers
don’t want employees to work harder, or faster – they want employees to work
more efficiently. Lean
manufacturing focuses on improving employees, providing more value to the
workforce, and, overall, establishing a dependable and stable workforce.
8.
Lean is Not about No Inventory
Lean
doesn’t mean ZERO inventory. Even with lean there may be a need to keep some
finished goods on hand or some inventory in a supermarket. It means the right
inventory at the right time at the right quantities and in the right place.
Every company needs buffers, but they must be well planned and controlled. Things
to consider are the demand of the customer and the time necessary to replenish
the material. Implementing a Kanban system for the supermarket or finished
goods helps to control the level and eliminates overproduction.
9.
Lean is Not Rigid
People
are often concerned that Lean efforts, including standardized work, will turn
them into unthinking robots. Many Lean methods are used so that abnormalities
are clearly visible and therefore can be reacted to. It is not about mindless
conformity. Lean creates a baseline so improvement can occur by freeing up
mental capacity from doing the routine in order to think about how the process
could work better. A truly Lean culture respects people and engages them in continuous
improvement.
10.
Lean is Not Mean
Company
executives that treat Lean as mean and use the tools to shed people, the source
of the company’s health, are either delusional or do not really care about how
the company performs in the long term. A Lean implementation that results in
layoffs should not be considered a successful Lean implementation.
Lean
is not easy. It's not easy to understand. It's not easy to implement. And it's
especially not easy to sustain. But anyone who has embarked on a so-called lean
journey already knows this. Lean, in fact, is hard work and it's a challenge to
keep it going.
Lean
is a process. It's a culture. It's a system. And at its core, Lean seeks to
optimize manufacturing processes and reduce or eliminate waste — everywhere in
the value stream.
But
Lean is not a quick fix and you cannot pick and choose the tools you use. The key to ongoing success is to embed Lean
as a philosophy, and a requirement in everybody’s role; ensuring the right
levels of line-management responsibility and accountability for gradually
implementing the various tools and techniques that support it.
Implementing
Lean, or any change initiative is difficult.
If it wasn’t, everyone would be doing it, and they’re not. The answer is that the philosophy, tools and
techniques are relatively simple, the hard bit is the culture, people,
training, employee acceptance and ultimately perseverance and endurance as
improvement does not happen overnight.

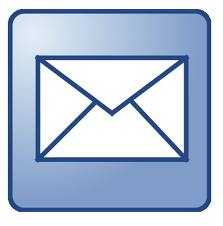





No comments:
Post a Comment