"Perseverance is not a long race; it is many short races one after the other." — Walter Elliot
Lean
is a journey that never ends. There will always be a gap between where you are
(current state) and where you would like to be (True North). Since there will
always be a gap, there will always be an opportunity to improve. Walking the
path on a Lean journey can be an overwhelming experience.
Lean
grew out of years of practice and experimentation at Toyota. No matter how much
better they are than their competition, they continue to find more and more
opportunities to improve each and every year. Lean involves the creation and
implementation of continuous experiments to improve your strategies over time.
This means experimenting with every process every day to get it right. We learn
problem solving through hands-on improvement experiments. In Toyota and in lean
thinking, the idea is to repeat cycles of improvement experiments forever.
A
Lean journey is full of steps not all of which are forward. Failure will occur.
Its ok, the purpose is learning, and we learn through experimentation. Trying new
approaches, exploring new methods and testing new ideas for improving the
various processes is exercise for the mind.
So
leaders must create a culture that puts failure in its proper place: a useful
tool for learning, and a natural part of iterative experimentation. Management
must avoid the temptation to harshly judge unsuccessful ideas. A leader who
allows for experimentation sends a clear signal that personnel are encouraged
to find better methods and products.
Organizations
embarking on a Lean journey should follow a disciplined process of systematic
exploration and controlled experimentation. Kaizen is the process which
determines whether processes resulted in improvements. It refers to an on-going
activity by all people (including managers) to relentlessly and incrementally
change and improve practices in small experiments.
The
road to continual improvement is a rocky one with many ups and downs. Value the
incremental improvement approach to continuous improvement. Through simple,
common-sense, and low cost experimentation a great deal of process improvements
can be made. Experimentation is the exercise of a healthy Lean journey.
Understanding this allows one the opportunity to stay on the path along the
journey.
Continuous
improvement is about small changes on a daily basis to make your job
easier. Small step-by-step improvements
are more effective over time than occasional kaizen bursts, and have a
significantly greater impact on the organization culture - creating an
environment of involvement and improvement.
Small
victories tap into motivation. Achievement is fueled by making small amounts of
progress, such as accomplishing a task or solving a problem. Help employees
break projects, goals, and work assignments into small victories. Help them jump
into an achievement cycle.
Making
one small change is both rewarding to the person making the change and if
communicated to others can lead to a widespread adoption of the improvement and
the possibility that someone will improve on what has already been improved.
There's no telling what might occur if this were the everyday habit of all team
members.
One
of the most counter intuitive facts about small ideas is that they can actually
provide a business with more sustainable competitive advantages than big ideas.
The bigger the ideas, the more likely competitors will copy or counter them. If
new ideas affect the company's products or services, they're directly visible
and often widely advertised. And even if
they involve behind-the-scenes improvements--say, to a major system or
process--they're often copied just as quickly. That's because big, internal
initiatives typically require outside sources, such as suppliers, contractors,
and consultants, who sell their products and services to other companies,
too. Small ideas, on the other hand, are
much less likely to migrate to competitors--and even if they do, they're often
too specific to be useful. Because most
small ideas remain proprietary, large numbers of them can accumulate into a
big, competitive advantage that is sustainable. That edge often means the
difference between success and failure.
In
a Lean enterprise a strategy of making small, incremental improvements every
day, rather than trying to find a monumental improvement once or twice a year
equates to a colossal competitive advantage over time and competitors cannot
copy these compounded small improvements.

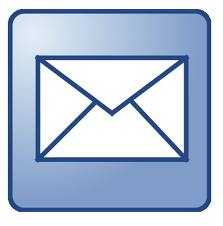





No comments:
Post a Comment