Lean manufacturing often focuses on the processes and employees. True lean manufacturing takes the entire facility into consideration. You cannot achieve your goal without looking at the equipment you are using. Here are some tips for optimizing your plant and leaning out your store of equipment.
Single
Minute Exchange of Die (SMED)
The
principle behind SMED, developed by Dr. Shigeo Shingo, is eliminating all wasteful procedures
when changing equipment over from one process to another. Without a
quick-change ability, manufacturers would run all batches of one unit before
changing tooling over to the next stage of the production process. While this
does save time, it can create an inventory excess that detracts from lean
operation.
With
SMED, the external and internal tooling processes are separated into two
sections. While many tooling changes, the ones included in the internal
category, can only be performed while the equipment is idle, external changes
can be ready and waiting. Everything needed for a changeover will be ready and
in place.
Implementation
may involve having a second employee ready the tools while the operator is
finishing the batch in process. Having additional sets of tooling, that account
for a size or tolerance difference, will improve the changeover speed.
Standardizing both the equipment and the tooling improves the ability to simply
remove and replace components as the work procedure changes.
Maintenance
procedures to limit failures
Regular
maintenance is critical to keep equipment operational. How you go about the
maintenance will depend on your production choices, but the work must be
performed. Some facilities will schedule set out-of-service times; others will
shut down production for up to a week every few months.
In
addition to following your set maintenance
schedule, have all equipment inspected on a daily or shift basis. At the
first sign of a problem, take the equipment out of service and have it
repaired. Continuing to operate a piece of machinery showing signs of failure
can lead to more damage and higher repair costs. You may also sacrifice the
quality of your product, leading to a higher cost in waste.
Purchasing
the right equipment
When
you purchase equipment and replacement products, take the time to make sure
that you are buying the quality you need. For example, replace worn wires and
cables with ones designed to withstand harsh operating conditions.
If
you can expect a 50 percent longer life span from a cable designed with a
high-flex life and superior resistance to abrasion and chemicals, you are not
only saving on the cost of the cable, but also on the labor involved in
replacement.
Simply
put, any breakdown of your equipment is costly. Consider the cost of the labor
needed for repairs, the cost of the parts and the loss of production. When you
look at it this way, the equipment you are using becomes a larger part of your
lean manufacturing goal.
About the author:
Scott McNeill is the Director
of Operations at TPC Wire
& Cable Corp. in Macedonia,
OH. TPC Wire & Cable is a leading supplier of wire, cable and connectors
used in manufacturing. TPC’s products are designed and engineered to withstand
harsh conditions including extreme temperatures, constant flexing and abrasion.

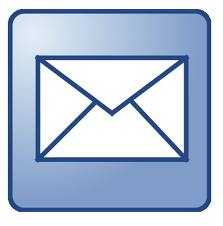





No comments:
Post a Comment