5S
is a process and method for creating and maintaining an organized, clean, and
high performance workplace. It enables
anyone to distinguish between normal and abnormal conditions at a glance. 5S can be the foundation for continuous
improvement, zero defects, cost reductions and a more productive work
space. The 5S methodology is a
systematic way to improve the workplace, processes and products through
employee involvement.
1.
Start small
It
would be unwise to try to implement 5S throughout your entire organization in
one go (unless you have a small company), better to select one area in which to
concentrate your efforts and provide a show piece for the rest of the
organization. In my mind it would be best to select the worst area in the
company so as to show what can be achieved and the differences it can make.
Showing success in one area gains the confidence of others and a reason to
buy-in.
2.
Training
The
whole team should be trained in the vision and objectives of the company and
given a clear understanding of what the company is trying to achieve through
them and their 5S program implementation. They need to have a clear understanding
of the seven wastes of lean and an overview of basic lean principles. With this
knowledge they will be ready to undertake their 5S implementation.
3.
Leadership buy-In and commitment
Your
management should understand and practice the ideas of 5S themselves so as to
provide an example to your other employees, it would be hard to motivate your
employees to keep a tidy workspace if every time they walked past their
managers desk they saw piles of untidy clutter. Management needs to be ready to
explain and help fix any situations that arise.
4.
Don’t make it stand alone
Doing
5S is liberating. We have all
experienced that feeling after cleaning the basement or garage after a year of
accumulating stuff. But 5S is just one
tool that enables stability that enables flow.
Well organized and sparkling clean waste is still waste. Getting bogged down in 5S can be an avoidance
pattern - avoiding the hard work of thinking about how to create flow and solve
the real root cause problems inhibiting flow.
5.
Monitor, review, and improve
Once
the team has completed the first activities they’ll need to focus on
sustaining. The team should create standard audits to assess and score their
area so that they can be monitored on an ongoing basis. In addition, the team
should meet to review how things are working and what additional improvements
they could make. Photographs
should be taken of the improved work area and a 5S story board put up to show
the improvements gained. I would also suggest that the team be allowed to make
a presentation to the management and the rest of the organization to show off
their achievements.
The
5S system is a good starting point for all improvement efforts aiming to drive
out waste from the manufacturing process, and ultimately improve a company’s
bottom line by improving products and services, and lowering costs. Many
companies are seeking to make operations more efficient, and the concept is
especially attractive to older manufacturing facilities looking to improve the
bottom line by reducing their costs.

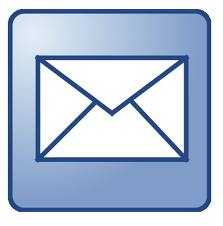





Hi Tim
ReplyDeleteI personally have a couple extra suggestions, and it comes ahead of the others. First is standardize how you handle your 5S decide when to tape or paint markings, what colors to use for what, how labels should be designed and how they should be positioned, how to document and display each area, and lastly how clean supplies and equipment should be stored. Second is related to each area you tackle. start with standardizing the work in that area, after all it will help clearly define what does and does not need to be there, and secondly in vastly improves and drives how you layout the area.