One
of the most common questions I hear with 5S (and Lean for that matter) is how
do you sustain. Sustaining 5S can be
very difficult without the use of 5S standard. A layered audit program is
essential to ensure that your company’s 5S efforts continue.
Layered
Audits are tied directly into the fifth S – Sustain – and they are the means
used in Lean Improvement Systems to avoid “backsliding” into old habits,
creating sustainable culture change.
Originating
in the automotive industry, the concepts behind the Layered Process Audit are
not new. They find their origin in the
well-known Plan-Do-Check-Act continuous improvement cycle.
The
key is everyone is an “auditor”. To
paraphrase E. Edwards Deming, no one goes to work with the intention of doing a
bad job. Therefore, everyone wants to
know that he or she is doing a good job. If people need to know that they are
doing a good job, they need to have metrics regarding their job. This starts with the operator personally checking
their process for compliance. Then the
first line supervisor checks key processes, where feedback is immediate as are
any agreed-upon corrective actions. The next level supervisor would then make
the same checks, and so forth, up the chain of command in the organization.
The essential part of the Layered Audit is the
creation of a standard checklist You
must identify and ask the right questions on the checklist. This is where Standard work at all levels of
the organization is critical. Layered Audits
is a formalization of “management by walking the Gemba”.
Layered Process Audits can be compared to a
preflight checklist. Is my operation ready for take-off? Am I confident that everything is in place to
build and ship conforming product to my customer? When the flight, or day, goes smoothly,
management and operators can use the time saved to work on improvements.
The
Layered Audit approach is especially effective in sustaining process
improvements and institutionalizing key process steps because all levels of the
organization participate. Managers often
can learn much about the manufacturing processes from operators, and operators
can learn much about what is important to customers from managers.

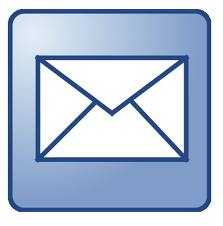





Thanks for the graphic and reminder about how important audits are to sustaining lean efforts. An audit timetable is key also.
ReplyDeleteI love it! Great discussion on sustaining 5S - regular review truly is key to maintaining best practices!
ReplyDeleteOne thought: Often the term "audit" has such an ominous cloud around it, I like to use different terms to avoid an unnecessary reaction. Saying "assessment" or "survey" or "review", depending on your organization, might lessen the negative reaction.
The important part of your message is the people in the various layers knowing what they are looking for, so deviations are more visible. And regular discussion surrounding the cause for deviations helps to uncover new best practices, because sometimes people deviate because they found a better way to do things.