Today I am pleased to be able share a guest post sponsored by one of our sponsors 9001 Academy. This post compares two product recalls in terms of a quality management system.
Product recalls
are something we have become used to in our society. As I argued in my article Does a
QMS ensure 100% quality?, product recalls do not mean that
there is a complete failure of the quality management system. In fact, the
existence of requirements for a process to deal with non-conforming products is
evidence that the ISO 9001 standard expects that
an organization will need to deal with products that do not meet requirements;
however, this process can either work well or be flawed. This article looks at
two recent examples of the non-conforming product process as it deals with
product recalls in the automotive industry.
What is needed in a non-conforming product process?
First, let’s look quickly at the requirements for
a non-conforming material
process, in particular, the requirements of what needs to be done to deal with
a non-conformance when one is identified. In Section 8.3, the ISO 9001 standard
requires that the organization take action to deal with an identified
non-conforming product in one of four ways:
1.
Take
actions to eliminate the non-conformance
2.
Authorize
use with acceptance from the customer when needed (intended for
non-conformances that do not hinder the operation of the product or service)
3.
Take
action to preclude original use (scrap or use as “seconds” where this is acceptable)
4.
Take
action to eliminate the effects of the non-conformity when it is detected after
delivery, or when use of the product has started
It is requirement
4 that could trigger a product recall if a repair needed to be made to the
delivered product. The next two examples demonstrate where this failed to
happen quickly enough, and when it has happened in a timely manner.
For more
information on the process for non-conforming material, see this blog post on Five
Steps for ISO 9001 Nonconforming Products and this blog
post on Understanding
dispositions for ISO 9001 nonconforming product.
GM ignition switch defects: When the process failed
In February 2014,
General Motors (GM) instituted a recall of 2.6 million vehicles worldwide for a
problem with defective ignition switches. The defect with this product is that
the ignition switch can slip out of the “on” position while driving, which can
lead to the car stalling and the air bags turning off. As of October 2014, this
has caused 27 deaths and many more injuries, leading to compensation claims
against the company along with the expense of the recall itself.
News reports state
that GM has acknowledged that it knew about the faulty ignition switches in
several of its small cars for over a decade before the recall was initiated. It
is clear that in this case, the decision on taking action on non-conformities
that were already delivered was not timely.
GM sunroof recall: When the process works
Just over a year
later, in March 2015, GM issued a recall for Chevrolet Malibu models due to
overly sensitive controls. This followed a recall of Cadillac ATS models in
February 2014 for the same issue. The controls in question would cause the
sunroof to close with only a slight touch of the controls. According to the
company, it does not take much force on the controls for the power sunroof
button to make the sunroof close, which could pose a safety hazard such as
fingers being caught in the closing unit.
In this case,
there are currently no known injuries from the defect, nor has GM received any
customer complaints, but still the recall was issued to address the problem.
Clearly, the process to address non-conforming products has addressed delivered
product as it is intended to do.
Make sure you address all non-conforming products or
services
The key point is
that a process for non-conforming products needs to address all products
or services when your company identifies a problem. Sometimes it is easy to
forget that products or services that are already delivered need to be included
when you are making your decisions on how to address a problem. In many cases,
there may be no action needed for a product or service already delivered, but
the decision on these products and services that are already in the hands of
your customers needs to be made and properly recorded. You owe it to your
customers to consider them in your dispositions, and customer satisfaction is a
key reason to have a quality management system in place.
About the Author:
Mark Hammar is a Product Assurance Manager and freelance author. Positions include working in all aspects of Product Assurance, including Supplier Quality Engineer, Quality Engineer, Product Assurance Program Manager, and Quality System Auditor. He is certified with the American Society of Quality as a Certified Manager of Quality and Organizational Excellence. His goal is to work more in Quality Management including supervision and people management.

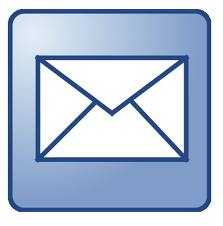





No comments:
Post a Comment