"Many hands make light work." — John Heywood
A
common saying we have all heard about teamwork that means the more people that
do a job, the easier the job for each person.
This is true in Lean.
Continuous
improvement is about small changes on a daily basis to make your job
easier. Small step-by-step improvements
are more effective over time than occasional kaizen bursts, and have a
significantly greater impact on the organization culture - creating an
environment of involvement and improvement.
Lean
is meant to involve the whole company. It is not intended to be put into action
in only one area. It is a management philosophy which should include every part
of your organization. This helps promote the concept that everyone in the company
is part of the team. True Lean manufacturing needs the involvement of everyone
coming into contact with the company’s product and its customer.
Improvement
should be ongoing and employees should be a critical part of that process so
there is not fear of change but a willingness to embrace it because it’s a part
of the everyday process in the organization. As employees begin to demonstrate
a willingness to assimilate change into their daily routine, they develop a
commitment to the change, a willingness to stick to the plan of action. The change actually becomes integrated into
the work environment, and employees begin to feel a sense of satisfaction in
accomplishment. They readily see the
payoffs associated with the change. They
enjoy, and may even take credit for, their participation in the process. Employees can view their efforts to bring
about change with personal respect and pride. The change becomes a part of
their routine, and any lingering concerns vanish.
In
Lean we strive for a culture in which everyone in the company makes small
improvements to their work environment everyday. Many organizations start with large
activities with titles like Kaizen or improvement events. This is necessary in the beginning to create
the conditions for change. You need to
teach people how and why to improve. The
Kaizened area then serves as a powerful example for the rest of the
organization to learn from. But as we
strive for "True North" we want to create an environment where
continuous improvement occurs regularly as part of the work.

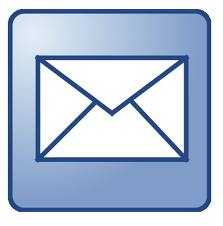




No comments:
Post a Comment