"Quality comes not from inspection but from improvement of the process." — Mary Walton
Unfortunately,
there are not enough organizations that understand quality. Quality is not
additive or final. It must go beyond the product or service. We cannot add it
at the end of the line or inspect it into the product. At best that is only a
false sense of security. If we want a quality product it must be made with
quality processes by quality minded people.
Nothing
is perfect and everything can be improved. We must continuously review how and
what we do in order to find better ways of doing it. This means accepting the
occasional mistake and having the courage to admit it, along with the strength
of mind to find a better way of doing things in the future.
Generally
the most effective way to achieve quality is to avoid having defects in the
first place. It is much less costly to prevent a problem from ever happening
than it is to find and correct the problem after it has occurred. Focusing on
prevention activities whose purpose is to reduce the number of defects is
better. Companies employ many techniques to prevent defects for example
statistical process control, quality engineering, training, and a variety of
tools from the Lean and Six Sigma tool kit.
Process-centric
thinking does not have to be overly complex. Sometimes, all it takes is a
thoughtful examination to uncover significant areas for improvement. Rather
than tolerating mistakes and repeat errors, facilitate process-centric thinking
to continually improve, correct, and overcome execution difficulties.
Start
with the idea of preventing defects, not waiting until they are identified and
correcting them. Many companies have an active Zero Defects policy where defect
prevention is paramount and quality inspection is almost just a verification of
what they already know – that the product is defect free. If we can start with
quality and maintain that quality throughout the process we will have a quality
product.

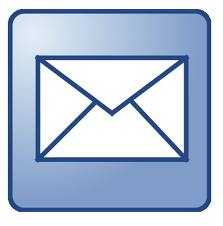




Quality minded people, I love that concept. One good example can be Safety. You cannot wait until a risk becomes an accident to take preventive actions.
ReplyDeleteGreat articule, thanks Tim.