When adopting new habits, it’s always a good idea to start with small changes, and work your way up over time. For example, instead of starting an intense paleo-diet, start drinking a glass of water before every meal to increase metabolism. Or, instead of beginning a rigorous workout plan, start walking around the block a few times every morning. Small lifestyle changes will not only lead to bigger changes over time, they will come more naturally and will be much easier to adopt into your routine.
Don’t
try to change the world all at once. People don’t like that – especially if
they can’t see why it’s important. Start with one small, easy area. Trying to
do too much when introducing a new process can be overwhelming. Too many times
we try to over complicate processes, events, projects, and even standard
work. Simplicity is the key to effective
continuous improvement. When we add levels of difficultly and complication we
add an opportunity for error and costs, and possibly waste.
According
to Occam's razor, all other things being equal, the simplest theory is the most
likely to be true. A simple solution
always takes less time to finish than a complex one. So always do the simplest thing that could
possibly work next. If you find something that is complex replace it with
something simple. It's always faster and cheaper to replace complexity now,
before you waste a lot more time on it.
Continuous
improvement is about small changes on a daily basis to make your job
easier. Small step-by-step improvements
are more effective over time than occasional kaizen bursts, and have a
significantly greater impact on the organization culture - creating an environment
of involvement and improvement.
If
your process isn’t simple, it’s going to be very expensive, not very usable,
and probably not sustainable – put simply, it will fail. Whether evaluating new
processes, or determining which ones to re-engineer or discard, make simplicity
a key consideration. Remember this – usability drives adoptability, and
simplicity is the main determinant of usability.
Lean
is meant to involve the whole company. It is not intended to be put into action
in only one area. It is a management philosophy which should include every part
of your organization. This helps promote the concept that everyone in the
company is part of the team. True Lean manufacturing needs the involvement of
everyone coming into contact with the company’s product and its customer.
Large,
difficult, or complex goals can be both overwhelming and discouraging if
progress does not come quickly. The solution to both of these is to break the
big goal into smaller goals, actually creating a separate goal for each part.
By shelving some of the pieces until a later date, you can avoid feeling
overwhelmed or discouraged.
In
the world of business it’s not always about survival of the strongest, rather
those companies that adapt to change. Human nature is resistant to change, so
the entire organization must be involved in establishing company goals and
objectives. Small changes are not only easier to handle, but easier to maintain
and perfect. The ideal company will learn through small, incremental
improvements to the current state. Think of it like building a house. The foundation goes down first, then the
frame work, the roof, the electricity, the installation, the walls, etc.

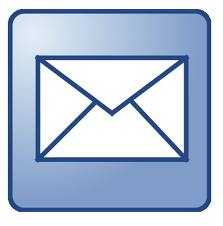





No comments:
Post a Comment