It can be
invaluable to learn from the creator of a system and the book “Management
Lessons from Taiichi Ohno” does just that. Takehico Harada is the author of
this comprehensive and informative guidebook into the Toyota Production System
(TPS) and to the man who invented it, Taiichi Ohno. Mr. Harada shares firsthand
knowledge of tools, techniques, and challenges to deploying Lean from 4 decades
of practice applying Lean principles.
The book was
translated by Brad Schmidt, a Lean consultant living in Japan. While written to
keep the integrity of the original he added his own comments and clarifications
to drive home key learnings.
The
book is organized into four chapters. In chapter 1 is a collection of 15
sayings directly from Taiichi Ohno.
These illustrate the importance of the role of top management in the
deployment of Lean.
Here
are the 15 ”sayings” of Taiichi Ohno that Harada wrote down, each of which he
discusses.
1.
“No One Really Understood What I was Saying, So I had to Go to the Gemba (“the
real place”) and Give Detailed Instructions” (7-11)
2.
“Kaizen Equals Getting Closer to the Final Process” (11-17)
3.
“You Need by the [Assembly] Line Only the Parts for the Car You Are Assembling
Now” (17-20)
4.
“Building in Batches Stunts the Growth of Your Operations (Don’t Combine
Kanbans [improvement systems] and Build a Group of Them” (20-24)
5.
“Nine Out of Ten, One Out of Ten” (24-29)
6.
“The Foreman or Leader Is the One Who ‘Breaks’ the Standard (When You Make an
Improvement and You Can Take Out One Person, Give Up Your Best Person” (29-32)
7.
“Multitasking Means Learning the Next Process — Keep It Flowing Until You Reach
the Last Process” (32-35)
8.
“What’s That Red Circle on the Top Right of the Graph?” (35-39)
9.
“Are You as the Manager Having Them Do It, or Are They Just Doing It Their Way?
Which Is It, Man?”(39-41)
10.
“Standard Work for the Andon [indicator of a problem] Is, ‘Go There When It
Flashes'” (42-45)
11.
“Standard Work Is the Foundation of Kanban” (45-49)
12.
“When the Worker Pushes the Start Button, He Has Stopped Moving. Can’t You Guys
Figure Out a Way to Push Start While Still Moving?” (45-52)
13.
“You Bought an Expensive Machine, and Now You Want an Expensive Foreman or
Engineer to Run It? Are You Mad?” (52-55)
14.
“Engineers in Production Become the Horizontal Threads in the Cloth” (55-60)
15.
The Lowest Kanban Quantity Should Be Five” (60-63)
Chapter
2 goes into more detail on what exactly top management should do and how to go about
doing it. Harada introduces the four categories of things:
- Waiting
- Being Inspected
- Being Transported
- Being Processed.
All
four of these are needed to complete things however only processing increases
value, others just increase cost. Management must understand this way of
thinking.
Chapter
3 is about the role of the front line manager. This chapter underscores the
importance of having a vibrant and happy workplace to motivate and empower
employees. Harada stresses the importance of mutual trust and team work to
effectively implement Lean. If you want a successful deployment, then it is
imperative that you value the concept of “all of us doing this together,
helping one another out, and doing it at the same pace.”
Chapter
4 covers how one would deploy Lean. Instead of a hard road map to
implementation, this versatile guide offers a flexible approach with:
- Expert tips for implementing 5S
- A step-by-step action plan for
changing organization to align with kaizen principles
- Management techniques for growing
employee empowerment and motivation
- Effective strategies to assess flow
and decrease waste
- Approaches to encourage Lean in and
outside of your company including suppliers
At
only 156 pages this book is a quick read which should be desirable for the target
audience, managers. The top management and middle management play a very
crucial role in ensuring the success of Lean deployment.
I
highly recommend Takehico Harada’s
Management Lesson from Taiichi Ohno a must read guidebook for change managers
in any organization. It fills in the leadership gaps that are needed to make
Lean sustainable.

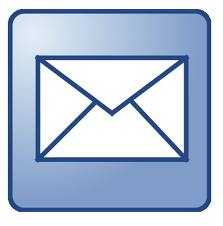





No comments:
Post a Comment