"Don’t be too busy mopping the floor to turn off the faucet!"
Whether a company has just switched to Lean
production or is still using a traditional manufacturing approach, if it does
not establish an official improvement time policy, very little improvement will
ever happen there.
We have seen this everywhere, even in companies
which loudly proclaim their commitment to continuous improvement. Little or no
actual time is set aside to do the very improvement the company says it wants.
It is an age-old battle — production time
versus improvement time. Two worthy rivals attempting to occupy the same narrow
24-hour space. The issue is not which is more important. Production is! This is
as it should be: a company is in business to sell its products and services. It
must first make them. And that takes time. Production time always comes first.
Without an improvement time policy, however,
the danger is that needed improvements will never happen.
Too often improvement is left to chance and the
ingenuity of the willing to eke out small pockets of time — and make magic
happen. We all know these people. They see the vision burning brightly before
them and are determined to make it happen. Time and again, these people prove —
with their own mental, emotional, and physical health — the familiar adage:
Where there’s a will, there’s a way.
In a sad and important way, these quiet heroes
do their companies and the rest of us some bit of harm. When they make magic
happen, in the absence of a clearly defined, improvement time policy, they
unintentionally send the message that separate time is not needed. Wise,
indeed, is the company that sees through this double-think and takes steps to
establish the policy nevertheless.
Improvement doesn’t just happen. It takes time, and in the pressure pot of our
day to day activities, there is never enough time to improve our situation. The
structure of Lean permits and requires time be set aside for improvement. If
managers do not definitively provide time for the task of improvement, then
people will know that they are not serious about making improvement a formal
part of the work.
Most of us don't set aside time in the day,
much less the week, just to improve. It doesn't take much time or skill, mainly
just will. We need to be encouraged and reminded that it only takes a few
minutes to do kaizen. Without assistance from management, people have no good
way to make time for improvement within the workday.
There can be no improvement without the time
and resource commitment from management to solve problems.

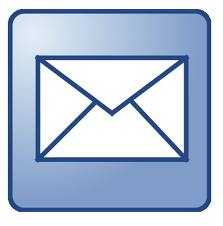




No comments:
Post a Comment