"It does not matter how slowly you go as long as you do not stop." — Confucious
Lean Thinking is often described as a “journey, not a destination”. In many regards this is true since the best Lean companies have found that their improvement efforts never end. Each set of improvements result in improved bottom-line results but also exposes more opportunity.
Lean is a journey that never ends. There will always be a gap between where you are (current state) and where you would like to be (True North). Since there will always be a gap, there will always be an opportunity to improve. Walking the path on a Lean journey can be an overwhelming experience.
This journey toward dramatically improved business performance shares three characteristics with more traditional travel. Every journey has a starting point, an objective, and a path that connects the two. In order to gain the maximum return on limited resources organizations must understand and optimize these three essential characteristics.
A Lean journey is full of steps not all of which are forward. Failure will occur. Its ok, the purpose is learning, and we learn through experimentation. Trying new approaches, exploring new methods and testing new ideas for improving the various processes is exercise for the mind.
The road to continual improvement is a rocky one with many ups and downs. Value the incremental improvement approach to continuous improvement. Through simple, common-sense, and low cost experimentation a great deal of process improvements can be made. Experimentation is the exercise of a healthy Lean journey. Understanding this allows one the opportunity to stay on the path along the journey.
Lean is a journey that never ends. There will always be a gap between where you are (current state) and where you would like to be (True North). Since there will always be a gap, there will always be an opportunity to improve. Walking the path on a Lean journey can be an overwhelming experience.
This journey toward dramatically improved business performance shares three characteristics with more traditional travel. Every journey has a starting point, an objective, and a path that connects the two. In order to gain the maximum return on limited resources organizations must understand and optimize these three essential characteristics.
A Lean journey is full of steps not all of which are forward. Failure will occur. Its ok, the purpose is learning, and we learn through experimentation. Trying new approaches, exploring new methods and testing new ideas for improving the various processes is exercise for the mind.
The road to continual improvement is a rocky one with many ups and downs. Value the incremental improvement approach to continuous improvement. Through simple, common-sense, and low cost experimentation a great deal of process improvements can be made. Experimentation is the exercise of a healthy Lean journey. Understanding this allows one the opportunity to stay on the path along the journey.

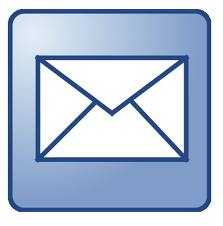




