Lean has been
around since the late eighties/ early nineties, but despite the enormous
popularity of Lean, the track record for successful implementation of the
methodology is spotty at best. Companies still make mistakes when implementing
Lean.
These mistakes
are generally due to simple misunderstandings of the Lean principles, but when
something goes wrong, you will not reap the full benefits, and incorrect use of
Lean can actually make a situation worse rather than better.
I believe when
Lean principles are properly understood and applied, the upside for
productivity improvements is nearly infinite. I have personally witnessed
numerous Lean thinking initiatives that have improved productivity by large
amounts (like 40-60%) in short periods of time with minimal expenditures.
The Lean track record is well documented by numerous authors.
In my
experience these are ten reasons why Lean implementation fails:
- No Strategy
Companies must
determine ahead of time what the vision and direction will be. A proper
strategy must assign clear responsibilities and show what resources are to be
committed. Metrics and timelines must be defined. Management must decide what
core elements are to be deployed and the order of deployment. They also must
determine where to start and how Lean will expand throughout the operation.
Finally, the strategy should anticipate problem and recovery scenarios. This is
critical. Companies can fail by attempting too much. They also can fail by
attempting too little and assigning the initiative to a "backburner"
status.
- No Leadership Involvement
Lean requires
top-to-bottom leadership of a special kind. Lean leaders are firm and
inspiring, relentless and resilient, demanding and forgiving, focused and flexible.
Above all, they have to be smart and highly respected in the organization.
Every successful company has at least one of these leaders. These people must
be a passionate part of the Lean leadership team.
- Relying on Lean Sensei/Champion
Expertise obviously
is necessary. So is critical mass. There must be a sufficient amount of
knowledge among a sufficient number of people for lean to work initially and
spread. Further, the expertise must reside with line people as well as staff.
Everyday support must come from important, respected line managers who have the
most to gain or lose and have the power and authority to make things happen.
Reliance on an outnumbered staff expert who has no line authority to implement
lean simply is not realistic. Deployment and implementation can fail before it
starts without a strong implementation team.
- Copying Others
Some
enterprises think they will get desirable effects by applying Lean tools that
others have gotten great achievements. Successful implementation of any Lean tool
must be closely related to the management philosophy. So we can’t succeed by
imitating and copying practices of others indiscriminately, it must be combined
with local culture.
- Thinking Lean Is A Tool
Lean
implementation can not be treated as a delegated "project." Lean
manufacturing is not a project. It is a fundamental change in the value
delivery system. Top management must be in front of this.
- Lack of Customer Focus
Many companies
do Lean for internal cost reasons rather than external and customer-focused
reasons. The focus of Lean is on providing the customer with more value sooner.
Without customer focus, Lean management techniques are difficult to employ.
- Not Engaging Employees
Employee
participation in project decision making is a main principle affecting
innovation, productivity, and work satisfaction. Workers typically have
more complete knowledge of their work than does management; hence, if workers
participate in decision making, decisions will be made with better pools of
information.
- Not Educating Employees
Lean training
is crucial, obviously. But the content, level, and depth vary by the company
and its needs, activity, and function. It goes back to the business case.
Training needs to be appropriate for the Lean elements to be deployed.
- Lack of Understanding
Most management
teams don’t understand Lean. When we don’t understand something it is next to
impossible to support it. This lack of understanding of Lean by management
allows even the most subtle of things to derail Lean efforts.
- Conflicting Metrics
Lean requires
metrics that focus on the processes of value creation and their associated
costs. Traditional cost accounting techniques such as absorption, as well as
individual machine and employee performance, can cause a lot of non-Lean behavior.
Lean accounting ties directly to financial measures but focuses on performance
of the entire value delivery system.
Lean
implementation is not simple or easy. However, results show that, when done
properly, Lean lives up to its promises. Lean and its elements work. All of the
failure modes presented here can be avoided or overcome.
If you want
Lean to succeed in your organization, management has to become a student of
Lean in order to be a successful sponsor. In other words, you have to apply
Lean to your management process first in order to understand how to apply it to
others.

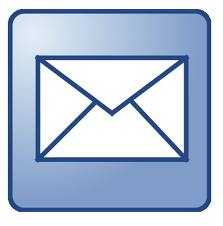





Yeah I agree to with you Tim McMahon , These all really create a big hurdle in six sigma or Kaizen Training process, thanks for sharing these beautiful lines, I'll surely look at this when ever I need to do Lean Implementation, thanks keep sharing dear...
ReplyDelete