Last week I spent several day in Chicago, IL, at IndustryWeek Inaugural Manufacturing and Technology Conference and Expo. IndustryWeek, MESA International and the Smart Manufacturing Leadership Coalition (SMLC) collaborated to provide the event on Smart Manufacturing, best practices from best plant winners, lessons learned from business leaders and practitioners.
Summary:
I would rate the Conference a 3 out of 5, or average. There were about 500 attendees with 70 exhibitors so it is considered a small or regional conference. The conference did include a plant tour and a workshop session which was beneficial. The location was very convenient close to O’Hare where the convention hall was connected to the hotel.
Much of the conference was centered on IT and software integration in business.
Plant Tour:
I visited Camcraft, a 2015 Industry Week 2015 Best Plant Winner, who manufactures precision-machined components for automotive fuel systems and hydraulics. Key points of tour:
- E2B2 (Everybody Every day getting Better and Better) continuous improvement program engages 100% of employees, producing over 5,000 completed improvements in 2015.
- A cadence of daily, weekly, monthly, quarterly, and annual meetings used to repeatedly measure performance, identify gaps, highlight waste, and encourage thousands of improvements from our empowered employees.
- Extensive robotics and automation paired with the latest machining and measurement technology. 10% of Sales reinvented in business annually.
- Real-time machine monitoring software (Mattec) used to measure and improve machine performance. Operator interface at machine.
Workshop:
I attended “How to Facilitate Effective Problem Solving (PDCA)” by Michael Thelen. The session focused on facilitation skills for leading a RCA team. This was a hands-on session with everyone taking roles within the team from Facilitation, Driver, Passenger, Navigators, and Pedestrians.
Conference Highlights:
Billy Taylor, Director at Goodyear, had a motivating keynote on engaging and empowering people in organization. Make business results visible and easy to understand. Train people in basic tools. Empower them to make improvements. Reward success. It is not about the source of the ideas but the quality of the solutions.
Hoshin Kanri session – Develop break through objectives with SWOT analysis. Develop VSM to identify opportunities. Create a “STOP DOING” list of initiative. Hoshin Kanri is a selection process to the vital few. Monthly, Quarterly, Annually review cadence.
- Quantity does not equal quality of objectives
- Break through objectives are not continuous improvement – radical change
Lean Transformation Session – Lean failure comes from 1) too focused on tools 2) results focused not process 3) Forgetting companies past 4) Silos within organization 5) not communicating
7 must haves for Lean Transformation:
- Fit for Purpose – alignment of objectives across organization
- Pull vs Push - manufacturing processes
- Process focused – Focus on process and results will come
- Value Stream Alignment vs Silos – Think horizontal across organization not vertical
- Leverage vs Create – Leverage your best practices, what you do well
- Principles vs Tools – Focus on the why not on the what
- Clarity/Capability/Reinforcement – Answer the what’s in it for me question – keep reinforcing
Key Take-A-Ways from Conference:
- IT infrastructure and software are critical investments to data collection and analysis for improvements
- Training employees of basic tools/problem solving is necessary but allowing them time to solve problems is critical. This is where behavior changes.
- Hoshin Kanri process is about alignment, selection, and execution of objectives with a specific cadence.
- Most of companies have own assessment model for operational excellence to compare facilities and assess progress on journey.
- Continuous learning is vital for improvement. Benchmark others, especially outside your industry. A coach or mentor can be extremely helpful.

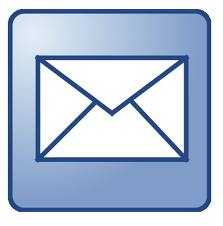





No comments:
Post a Comment