Click this link for A Lean Journey's Facebook Page Notes Feed.
Here is the next addition of tips from the Facebook page:
Lean
Tip #1411 – Make Suggestions Public
If
you have a locked box for suggestions, please take it down. They are a symbol
of a failed system from the past and they represent much that is wrong with
American suggestion systems. Why locked? To hide participation, to hide ideas,
to submit in secrecy, to not share ideas, … Make your Idea System public so
participate or lack thereof is visible to all.
Lean
Tip #1412 - Focus on Singles not Home Runs
Encourage
small ideas that can be implemented quickly by the employee versus large
changes that require external resources such as engineering, IT and facilities.
While some of these types are inevitable, they need to be balanced with many
more that can be completed within the unit.
Lean
Tip #1413 - Encourage All Ideas
Don’t
limit the number of suggestions by putting too many constraints. Let your
employees know that you’re interested in any suggestions that they think will
help the organization. As the Nobel Prize-winning chemist Linus Pauling said…
“The best way to
have a good idea is to have lots of ideas.”
Lean
Tip #1414 - Show Active Interest in Employee Suggestions
Most
employees wouldn’t continue to submit suggestions if their manager didn’t show
interest in the suggestions. Showing active interest in their suggestions can
encourage your employees to submit more suggestions that can benefit your
organization.
Lean
Tip #1415 - Share More, Not Less.
Even
in a small company, silos emerge. A policy of more sharing will help everyone
stay in touch with what others are doing, and create a collective expectation.
Keeping everyone pointed in the same direction is hard; sharing more about
what’s going on, how you’re doing things, reasoning behind decisions, etc. will
help.
Lean
Tip #1416 - Don’t Automatically Blame the Tool.
It’s
not the hammer’s fault if the person swinging it uses the wrong end. It just
won’t work well. Most tools are decent enough, they’re just used incorrectly.
Rushing to change a tool because things aren’t working well may be a mistake.
Lean
Tip #1417 - Process isn’t a Bad Word.
Lean
can certainly get too heavy-handed and top down in its implementation, but
without good processes in place your transformation will sputter along instead
of hum smoothly. Good processes and a way of continuously improving them serves
as a constant, in an environment of frantic change.
Lean
Tip #1418 – Leverage Leadership to Create Change
In
most organizations, employees follow leadership’s example. To create change,
executives, directors, and managers must be the champions of knowledge sharing,
transparency, and worker engagement. Dedicated personnel may give advice and
direction, such as internal communications managers. But senior execs,
department directors, and team managers need to back them up. This has to be a
collaborative effort.
Lean
Tip #1419 - Encourage Risk-Taking
Give
your employees the freedom to experiment, learn from their mistakes, and
succeed. Encourage them to take risks and think outside-of-the-box. Supporting
your employees for taking risks further encourages them to be creative.
Lean
Tip #1420 - Don’t Be Afraid of Mistakes
Mistakes
help you learn what works and what doesn’t. Let your employees know that it’s
totally okay to make a mistake. For many employees, the fear of making a
mistake stops them from sharing their ideas or even thinking up great ideas.
Letting your employees know that mistakes are okay, encourages them to share
the great ideas they may have.
Sure,
there will be mistakes. But some of those mistakes will turn into great innovations.
Lean
Tip #1421 - Think of How To Do It, Not Why It Cannot Be Done.
The
pessimist will create all kinds of reasons that something can't be done. The optimistic,
forward thinker, on the other hand, knows that "if the why is strong
enough, the how will come."
Focus
on the outcome. Then, come up with all the ways that the outcome could possibly
be accomplished.
Lean
Tip #1422 - Do Not Seek Perfection.
Do
it right away even if for only 50% of the target. If we all waited for
perfection, we'd still be reading by candlelight and riding horses to work.
Once you get to a certain point (whether it's 50% or 80%, or another number
that makes sense), then run with it. In other words, take action. Then, adjust
as you go along.
Lean
Tip #1423 - Ask "Why?" Five Times and Seek Root Causes.
The
question "why?" is extremely powerful. If a person has a strong
enough "why", he or she can accomplish anything. The question
"why?" can serve to either strengthen our conviction about something,
or help us to discover that it really wasn't as important as we thought it was.
At a minimum, it helps us to get to the root of the issue.
Each
time you ask "why?", you reveal a new layer. You go deeper, and
deeper. Then, after four or five answers, you'll get to the real one. Try it!
Lean
Tip #1424 - Do Not Just Spend Money for Kaizen, Use Your Wisdom.
It
is not enough to simply buy a tape set to learn skills, or to merely attend a
workshop or seminar. These are wonderful (and essential, in my opinion) first
steps, but action is key. Learn, yes. But then take action based on what you
have learned.
Lean
Tip #1425 - Seek The Wisdom Of Ten People Rather Than The Knowledge
Of
One.
Much
has been written about the power of group thinking. Whether it involves seeking
one or two other people's opinions, holding a meeting with others, or more
formal brainstorming or mastermind groups, there is power in numbers.
If
you want to find out how to be successful at something, as someone who has
already done it. Better yet, gather several people who have already done it.
With libraries, the internet, and other resources available today, we have more
opportunities than ever to gather the wisdom of others.

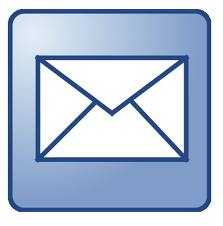




No comments:
Post a Comment