5S is a process
and method for creating and maintaining an organized, clean, and high
performance workplace. It enables anyone
to distinguish between normal and abnormal conditions at a glance. 5S can be the foundation for continuous
improvement, zero defects, cost reductions and a more productive work
space. The 5S methodology is a
systematic way to improve the workplace, processes and products through
employee involvement.
The five S’s
basically stand for seiri, seiton, seiso, seiketsu and shitsuke. Let’s briefly
go over these five terms in English for better understanding.
1. Sorting: The
first “S” stands for sorting, this essentially means to get rid of unnecessary
items or tools and to prioritize the items that are used so they can be stored
more efficiently and within accessible areas.
2.
Straightening: The second “S” is for straightening or setting things in order.
The main objective here is to organize the workspace to be most efficient and
productive by locating tools and equipment most often used in easy to access
areas. Not only does this better utilize the space within the work area, but it
also helps to save time that may be lost in trying to locate specific items or
tools.
3. Shine or
Sweeping: The third “S” focuses on cleanliness. Having a clean and tidy
workplace encourages others to also keep the area clean and helps contribute to
a more productive and effective work environment.
4.
Standardizing: The forth “S” helps with standardization, the goal with this
strategy is to keep workstations that do the same jobs more uniformly
organized. For example, if an employee does a particular job and there are
multiple work stations doing that same job, the employee should be able to move
effortlessly from workstation to workstation since they all function in the
same manner.
5. Sustain: The
fifth “S” is for sustaining the practice. This step basically includes the
monitoring and sustaining of the four previously mentioned 5S tactics. The
focus should be to move forward with the 5S methodology and not fall back into
old ways and habits that are potentially not as beneficial and effective for
the organization.
A Visual
Workplace - also known as Visual Factory or Visual Management – is a lean
concept that emphasizes putting critical information at the point of use.
Visual systems and devices play a critical role in many of the most popular
lean tools, including 5S, Standard Work, Total Productive Maintenance, Quick
Changeover, and Kanban (Pull Production).
In fact, Visual
Workplace serves as the key sustaining force for these initiatives, because it
ensures that Lean improvements remain clearly visible, readily understood, and
consistently adhered to long after the Kaizen or rapid improvement event is
over.
In my
experience there are 5 tools that can help with a Visual Workplace and 5S
efforts:
- Camera. Pictures are very effective at visually highlighting the improved appearance and order in the workplace.
- Laminator. Customize your own visuals with a laminating machine. The use of visuals helps to ensure that the new standards remain clearly visible, readily understood, and consistently adhered to by all employees long after the Lean or rapid improvement event is over.
- Label Maker. The right printing system can be an essential tool for creating an orderly and visually instructive workplace, allowing you to make signs, labels, tags, and more on demand.
- Communication Boards. Use communication boards to track key performance indicators, provide Lean activity updates, report audit / inspection results, and recognize achievements.
- Tape. Floor marking lays the foundation for the ‘set in order’ stage of 5S, as you start from the floor and work your way up organizing the facility. The proper use of floor marking tape helps create order and pattern of work in your facility, which eliminates searching and confusion within a work area. Floor marking also helps to clearly define processes and cells in the value stream.
In 5S, visual devices
like red tags, floor marking tapes, shadow boards, and shelf labels are used to
ensure that there is a place for everything - and everything remains in its
place after a kaizen event is over. Likewise, the Standardize and Sustain steps
of 5S are virtually impossible to manage without the use of visuals such as
check sheets, schedules and audits.

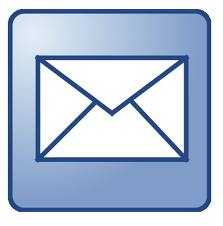





We apply this at my facility and works like a charm!
ReplyDelete