5S is a prerequisite for most other Lean tools. Well-implemented, 5S can open up entry points into flow and pull, equipment reliability, standardized work, and value analysis. 5S is a process and method for creating and maintaining an organized, clean, and high performance workplace. It enables anyone to distinguish between normal and abnormal conditions at a glance. 5S can be the foundation for continuous improvement, zero defects, cost reductions and a more productive work space. The 5S methodology is a systematic way to improve the workplace, processes and products through employee involvement.
The five S’s basically stand for seiri, seiton, seiso, seiketsu and shitsuke. Have I lost you? I hope not. Let’s briefly go over these five terms in English for better understanding.
1. Sorting: The first “S” stands for sorting, this essentially means to get rid of unnecessary items or tools and to prioritize the items that are used so they can be stored more efficiently and within accessible areas.
2. Straightening: The second “S” is for straightening or setting things in order. The main objective here is to organize the workspace to be most efficient and productive by locating tools and equipment most often used in easy to access areas. Not only does this better utilize the space within the work area, but it also helps to save time that may be lost in trying to locate specific items or tools.
3. Shine or Sweeping: The third “S” focuses on cleanliness. Having a clean and tidy workplace encourages others to also keep the area clean and helps contribute to a more productive and effective work environment.
4. Standardizing: The forth “S” helps with standardization, the goal with this strategy is to keep workstations that do the same jobs more uniformly organized. For example, if an employee does a particular job and there are multiple work stations doing that same job, the employee should be able to move effortlessly from workstation to workstation since they all function in the same manner.
5. Sustain: The fifth “S” is for sustaining the practice. This step basically includes the monitoring and sustaining of the four previously mentioned 5S tactics. The focus should be to move forward with the 5S methodology and not fall back into old ways and habits that are potentially not as beneficial and effective for the organization.
Insite Solutions recently created a game to help people learn Lean and 5S principles. The seen is a factory setting where you need to drive a fork truck to pick up certain loads. As you can see from below it is very difficult with the disorganized work space. You are timed for which you earn points for completed loads and loose points for hitting objects.
In the next step of the game you go through the factory and red tag items that aren't needed or don't have a home. This makes the area less crowded.
Finally, you create walk ways, add visuals for ease of communication, and create storage locations by grid. This makes moving through the factory very easy and quick. Picking the orders are simple because everything is easy to find.
I think this game illustrates a wonderful real world example. Frankly, one the that I see on a daily basis. This is a great learning tool for anyone in manufacturing and of course if is fun, too.

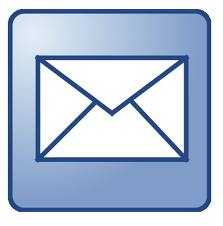





Tim! I work for InSite Solutions and just saw you featured our game! Thanks so much! We really like your blog - thanks for all the good information you are always putting out there.
ReplyDeletethank you so much nice info !!!!!
ReplyDelete