We all make
mistakes, to err is human. The question
is why does it happen and how can you prevent it. The essence of mistake-proofing is to design
both products and processes so that human errors or mistakes are impossible to
make or, at the least, they are easy and early to detect and correct. Poka-yoke
is Japanese slang for mistake-proofing, a term coined by Shigeo Shingo.
When performing
a mistake-proofing analysis on a manufacturing, service or business process, it
is of course important to identify every human error possible during each
process step. There are 16 human error modes particularly helpful to understand
when identifying potential human errors.
The Sixteen Human Error Modes
1.
Omission
What
part of the process is prone to be omitted?
2.
Excessive/Insufficient
Repetition
What
part of the process is prone to be excessively repeated?
3.
Wrong
Order or Sequence
In
what wrong sequence can the process be executed?
4.
Early/Late
Execution
What
execution can be early or late?
5.
Execution
of Restricted Work
What
tasks could be executed by unauthorized personnel?
6.
Incorrect
Selection (or Identification)
What
object of the process is prone to be incorrectly selected or identified?
7.
Incorrect
Counting (or Calculating)
What
objects of the process can be counted, measured, or calculated incorrectly?
8.
Misrecognition
(or Misunderstanding or Misreading)
What
misunderstanding or misreading is prone to occur?
What
information, risk, or failure/error is prone to be overlooked?
What
miscommunication is prone to occur?
What
incorrect decision is prone to occur?
9.
Failing
to Sense Danger
What
information, risk, or failure/error is prone to be overlooked?
10. Incorrect Holding
What
object of the process are prone to mishandling?
11. Incorrect Positioning
What
positioning setting error is prone to occur?
12. Incorrect Orientation
What
orientation error is prone to occur?
13. Incorrect Motion
What
motion or movement error is prone to occur?
14. Improper Holding
What
object of the process are prone to mishandling?
15. Inaccurate Motion
What
motion or movement error is prone to occur?
16. Insufficient Avoidance
What
can be unintentionally touched, stuck, or splashed?
What
movement can cause harm?
We must
approach human error by considering the interfaces of the process that the
operator is engaged in. The process should be designed to permit communication
between the process and the operator.
Shingo argued
that errors are inevitable in any manufacturing process, but that if
appropriate Poka-yokes are implemented, then mistakes can be caught quickly and
prevented from resulting in defects. By eliminating defects at the source, the
cost of mistakes within a company is reduced.

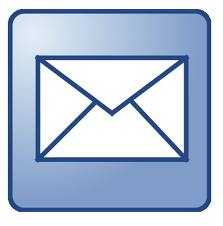





No comments:
Post a Comment