Generally the most effective way to achieve quality is to avoid having defects in the first place. It is much less costly to prevent a problem from ever happening than it is to find and correct the problem after it has occurred. Focusing on prevention activities whose purpose is to reduce the number of defects is better. The idea is to have processes and procedures in place that reduce or eliminate mistakes.
Mistake
Proofing is about adding controls to prevent defects, reduce their severity,
and detect them if they can occur. The concept was first put to widespread use
by Shigeo Shingo within the Toyota Production System (TPS).
The main aim of
mistake proofing is:
PREVENT a
defect from occurring and when this is not possible, DETECT the defect every
time one occurs.
Defects found
in later operations or steps of a process have more costs associated with them.
There are more materials, labor, overhead, previously reworked product that are
at risk. Ultimately if the product gets to the customer as a defect, the
intangibles, such as reputation, can exceed the tangible cost.
Poka-yoke
devices could be characterized by effectiveness:
GOOD: Detect
defect before proceeding to next step.
BETTER: Detects
defects while in process at an operation.
BEST: Prevent
defects from occurring at all.
The 7 best
poka-yoke devices are:
1. Guide Pins
Guide pins of
different sizes and/or shapes and placed in the proper locations ensure that
parts are being assembled correctly by providing the operator feedback when a
mistake has been made. Guide pins can also be used to ensure proper positioning
of the part.
Applications
- Proper alignment of a work piece
- Proper orientation of a work piece
- Easy to develop & implement
- May be the result of DFA and DFM activities
- Wrong order, incorrect selection, incorrect positioning, incorrect orientation
2. Error
Detection & Alarms
In general, an
error detection device can provide a visual alarm such as a flashing light or
an audible alarm such as a horn or siren.
These devices
signal that a problem is either about to occur or has just happened. With a
warning effect, the response is not automatic; someone has to take action.
Application
- The signal must be triggered by something in the process, usually a sensor.
Features
- For audible warnings, there are sirens, horns, bells, and even voice synthesizers.
- For visual alarms, there are lights that flash, rotate, strobe, or just light up.
Warning: If you
do use these warnings, the audible or visual signal must stand out from background
noise and lights. If audible alarms are used, be careful not to exceed noise
standards.
Be careful of
“alarm silence buttons.” It is easy to silence the alarm and then forget to
take action. Operators need thorough training on how to react to warnings.
3. Limit
Switches
Limit switches
are electro-mechanical devices that are activated or deactivated when an object
comes in contact with them. They are used to detect the presence or absence of
an object.
Applications
- Proper positioning of safety devices
- Detection presence or absence of an object
- Positioning of a work piece
Features
- Requires physical contact
Human Error
Prevention
- Omission, excessive/insufficient repetition, incorrect selection, incorrect counting, incorrect positioning, incorrect orientation
4. Sensors
A. Proximity
Sensors
Proximity
sensors emit a high-frequency magnetic field and detect an upset in the field
when an object enters it. They can be used to detect the presence or absence of
an object.
Applications
- Sensing of tank or bin level
- Confirmation of part or object passes by
- Detection presence or absence of object
- Positioning of work piece
Features
- Non-contact
- Work in harsh environments
- Small sensors are available for installation in tight areas
- Fast response speed
Human Error Prevention
- Omission, excessive/insufficient repetition, incorrect selection, incorrect counting, incorrect positioning, incorrect orientation
B. Laser
Displacement Sensors
Laser
displacement sensors focus a semiconductor laser beam on a target and use the reflectance
of the beam off the target to determine the presence of a target and distance
to it.
Applications
- Measuring distance
- Detection of presence or absence of a feature
- Confirmation of part or object passes by
- Positioning of work piece
Features
- Non-contact
- Works in harsh environments
- Some devices can achieve measurement precision down to 0.004 mils (0.1 um)
Human Error
Prevention
- Omission, incorrect selection, incorrect counting, failing to sense danger.
5. Vision
Systems
Vision systems
use cameras to look at a surface and then compare the surface viewed to a
“standard” or reference surface stored in the computer. They can be used to
detect the presence or absence of an object, the presence of defects, or to
make distance measurements.
Applications
- Missing of incorrect parts in an automated assembly line
- Poor quality surfaces or components
- Correct orientation of parts or labels
- Ensure correct relative position
- Color detection
Features
- Non-contact
- Need to have sufficient light
- Flexible (can be reprogrammed for a variety of applications)
- Compact systems are now available
Human Error
Prevention
- Omission, incorrect selection, incorrect positioning, incorrect orientation, misrecognition
6. Counters
& Timers
Counters
(optical or electro-mechanical) look at the occurrence of events. They are
usually triggered by some type of sensor. Counters can be programmed to shut
down the process if a set number of events do not occur or if too many events
occur. Timers can shut down the process if processing time or activity time
does not meet or exceeds a preset level.
Applications
- Ensuring the proper number of events occurred
- Preventing failure of equipment or a component usage
Features
- Flexible
- Easy to use
- Easy for people to understand
Human Error
Prevention
- Excessive/insufficient repetition, incorrect counting, incorrect positioning, incorrect orientation
7. Checklists
A checklist is
a type of informational job aid used to reduce failure by compensating or
potential limits of human memory and attention. It helps to ensure consistency
and completeness in carrying out a task.
Applications
- Shift Start-up
- Product Changeover
- Equipment Set-up
Features
- Easy to develop
- Easy to use
- Easy for people to understand
Human Error
Prevention
- Omission, early/late execution, wrong order, misrecognition
Post Courtesy of QualityTrainingPortal.com

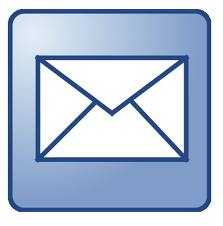





No comments:
Post a Comment