"Use every person's skill set to the fullest. Both optimist and pessimist contribute. An optimist invents the hot air balloon, and a pessimist invents the parachute." — Ramesh Lohia and Surbhi Lohia, Consultants, Six Sigma, Kaizen
The worst kind of waste is the lack of employee involvement and creativity. Lean doesn’t work unless everyone is involved and has input. We must involve employees in the continuous improvement process because the people actually carrying out the job know how to do that job better. The best companies in the world tap the creativity and talent of the whole organization and not just a select few.
The lack of ongoing employee involvement at the shop-floor level has been identified as a major reason for the non-sustainability of Lean in the organization. When there is a lack of staff involvement, and management fails to seek employee input on critical decisions, employees may feel dejected and detached from the organization.
This happens frequently in large organizations where the skills and backgrounds of everyone are not common knowledge. This can vary from not capturing ideas that employees might have for new products or innovations, to the six-figure salary executive correcting data entry errors in a financial spreadsheet. The biggest crime in this category is not empowering or enabling the people most intimate with a process to improve the process.
Lean thinkers at Toyota believe that showing respect for people means you allow them to think for themselves and solve their own problem. It is often said that the mission of Toyota is about developing exceptional people who happen to make great cars. The point is that it is more about people and less about the problem.
The lack of ongoing employee involvement at the shop-floor level has been identified as a major reason for the non-sustainability of Lean in the organization. When there is a lack of staff involvement, and management fails to seek employee input on critical decisions, employees may feel dejected and detached from the organization.
This happens frequently in large organizations where the skills and backgrounds of everyone are not common knowledge. This can vary from not capturing ideas that employees might have for new products or innovations, to the six-figure salary executive correcting data entry errors in a financial spreadsheet. The biggest crime in this category is not empowering or enabling the people most intimate with a process to improve the process.
Lean thinkers at Toyota believe that showing respect for people means you allow them to think for themselves and solve their own problem. It is often said that the mission of Toyota is about developing exceptional people who happen to make great cars. The point is that it is more about people and less about the problem.

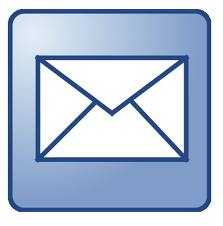





As individual talent and skills are highly important to be fully utilized and recognized it is also important to remember the true power lies with the teams to do things and to get things done. Respect and recognition of high achievement are very important aspects of team development to sustaining and creating higher out put work cultures.
ReplyDelete