A recent fortune
cookie fortune reminded me of an important Lean lesson. The fortune says:
“The best angle
from which to approach any problem is the TRYangle.”
I’ve learned at
Wiremold, originating from Art Byrne, the fundamentals of trystorming. This
method consists of, “Rapid cycles of real-time experimentation, used to test
and adjust improvement ideas before establishing standard work or implementing
processes broadly.” In plain language this means – try it out! Try Storming
incorporates physical actions that can engage other senses and give testers a
better sense of whether an idea is viable or not.
Trystorming is
different from brainstorming in that it encourages the rapid development and
test of an idea rather than merely thinking about the possible solutions. It
allows people to visualize, touch and further improve on an initial idea. It
also models action rather than talk. Often in our desire to design the perfect
Future State we forget that the best way to build a process that works is
through the iterative process of trying, adjusting/correcting, and trying
again.
The process is
built on three basic principles:
- It is not important to create perfect solutions.
- Be action-oriented.
- Keep solutions simple.
These
principles work hand-in-hand to develop effective solutions. When implemented
correctly, Try-Storming can be used to continuously improve any business
process.
One of the key
reasons to utilize trystorming as part of any process design activity is that
it models action rather than talk. By leaving the conference room and actually
trying ideas during the course of the work, your team will quickly realize that
your activity is more than just a meeting or an exercise in theory.
In
addition, taking action typically increases the level of idea generation and
team engagement exponentially. By mocking up and trying concepts the team will
be able to visualize their ideas and transform plans into tangible improvements
quickly. While trystorming requires much more energy than the traditional
design approach, use of this methodology will significantly reduce the overall
time needed to reach a workable solution.

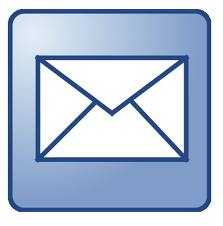





I found it was best to use the PCR process change request system. I provides control to the change process where it requires more team associates to become involved in the proposed change and then provides for the a trail run period, usually a week.. The PCR keeps things out in the open and does not allow for changes to the control plan with out the process engineer knowing. A PCR that goes through the one week trial period with both shifts agreeing is an improvement will be made a permanent change to the process.But remember to watch closely for unintended consequences.
ReplyDeleteI use a couple of quotes to try to help guide my efforts as well as those of my team - "Fail fast" and "Perfect is the enemy of good enough".
ReplyDeleteToo many times, we try to look for the ultimate solution rather than the one that gets the job done safely and effectively, which usually translates into a long computer design effort, catalog browsing, expensive metal cutting and then a first pass that's doesn't come close to meeting the needs of the operator. The process just goes downhill from there with respect to the ME-Operator relationship.
YES this is a great tool to move from meeting theories to action. However it must be very well controlled (specially when working with HiTech production equipment). We've implemented this tool in our factory and because improper implementation we end up undoing part of the mini-projects of improvement made by the operators. The non verbal communication (operator's perspective) was really bad, obviously demotivating, and really hard to overcome for the 2nd stage of the project implementation (not that hard to imagine). It's DEADLY important to have full control of the situation and make sure that proper limits are set when implementing such tool.
ReplyDelete